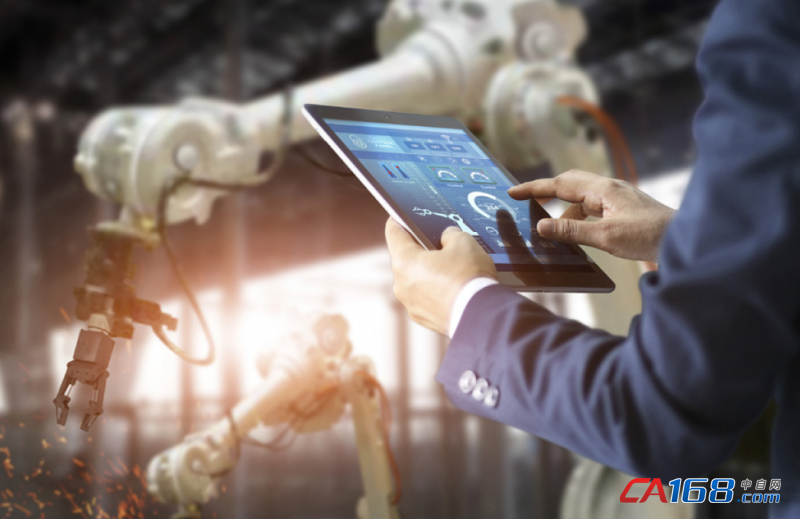
多年来,各级机器制造商一直致力于改善设备的换产时间和生产的灵活性。在实际的运营生产中,生产 SKU 数量与生产灵活性不断提高,而工厂的吞吐量运营却远远跟不上。因此,想要与换产生产速率保持一致,制造商就要牺牲一些设备的吞吐量,才能保持灵活的生产和充足的供应。然而,面对如今市场激增的需求,天秤迅速倾斜,工厂产量速率的增长可为企业带来更大效益,而这也给企业的灵活性带来了严峻的考验。
那么,如何在不影响吞吐量的情况下,构建更智能、更灵活的设备呢?罗克韦尔自动化给出了以下解决方案:
技术推动产业升级
在设备生产中,优化设备性能是重中之重,但许多制造商发现,对采用传统技术的设备进行逐步改进已经无法满足客户对于灵活性的需求。使用静态机械部件、摩擦式传送装置和众多辅助设备制造的机器以固定的变量生产统一的产品,或许可以实现较高的产量,但无论经过多少次设计更迭,这类机器往往都无法达到“多品种、小批量”环境下的生产力目标。
既想要设备灵活性的提高,又能带来产量的提升得益于机电一体化技术的发展。在装配、包装等领域,以下技术的主导作用显得尤为重要:
机器人技术
机器人具备固有的灵活性,在无需机械改道的前提下,既可以通过视觉引导型巡线技术来处理变化无穷的产品形状和尺寸,还可以在满足生产效率的同时随时更改配方。
独立小车技术 (ICT)
传统的传送系统以固定速率让产品在预先配置的路径上移动,而 ICT 则根据小车在系统中的定位,灵巧地调整其他小车位置,极大地提高了生产的灵活性和产量。
自动换模
由于机电一体化取代了复杂的机械设计,机器设备能够以更少的零部件实现更多的工作方式,占用的空间也大大缩小,在仿真和数字孪生技术的帮助下,设备制造商可以在虚拟环境中测试和确认设计,从而加快创新,减少风险。更多的原始设备制造商 (OEM) 开始通过统一机器控制策略将这些技术集成至其设备和工厂架构中。
数据优化与时俱进
升级设备以提高其信息实用性,是帮助客户提高成功几率的重要方法之一。这意味着需要打造标准化的控制平台和网络基础设施,从而简化集成过程并安全高效地连接至分析平台和业务系统。
工作人员往往通过警报提示来优化维护流程,延长设备的正常运行时间。如果系统发出警报,说明触发了电机过载,但是面对产生电机过载的原因,工作人员仍要对其作出多个决策判断。如果将历史数据库连接进到网络,那么分析工具就可以创建模型,根据模拟数据的表现预测未来的行为,并利用处理器学习功能来优化操作,为操作员创造采取预防措施的时间,或者可以让设备自动采取指定措施(例如让电机减速),以便保持阈值并使设备持续运行。
罗克韦尔自动化以先进的技术赋能制造业发展,为制造商提供更智能、更高效的数字化技术解决方案。重新定义系列(上集)结束,请继续点击重新定义系列(中集)探索在科技的迅速发展下如何实现高效且灵活的生产运营模式。