“碳达峰”、“碳中和”成焦点
“碳达峰”、“碳中和”,实际上,这出自于2020年第七十五届联合国大会上中国向世界的郑重承诺——力争在2030年前实现二氧化碳的排放总量达到历史峰值(即“碳达峰”),并努力争取在2060年前实现“碳中和”。
“碳达峰”、“碳中和”的目标都是“控碳”,这对于地球气候变化、人类生存环境的未来发展起到至关重要的作用,中国作为目前全球最大体量的制造业国家,在其中承担的责任责无旁贷,也必将对国内产业结构布局、能源结构调整、新能源开发利用产生重大的影响。
“碳中和”,简单来说就是通过节能减排的形式,以抵消自身产生的二氧化碳或温室气体排放量,达到相对“零排放”。围绕“碳达峰”、“碳中和”,目前国内的改革路径大体从三个方面来实现:工业减排、环保检测、新能源使用(图1),背后则是能源革命、能源安全、能源责任三大内在驱动力,在供给侧、输配侧、需求侧涵盖多个产业行业,需要在大幅提升能源利用效率、大力发展新能源与可再生能源等方面进行科技创新。
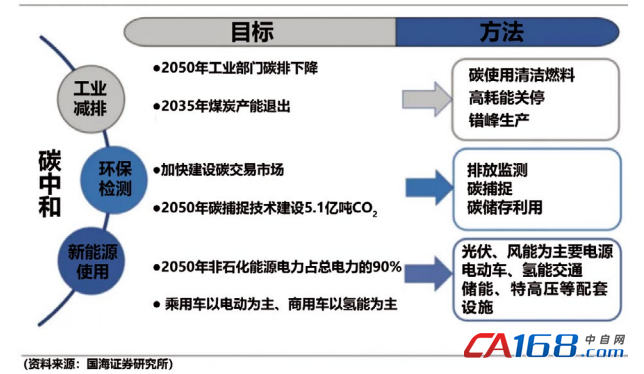
图1碳中和实现的路径
以现阶段国内新能源的开发与使用为例,其中主要包括:电力系统通过光伏、风电来实现无碳发电;以及交通运输系统大规模电动化/氢能化。经过近十余年的发展,中国光伏、新能源汽车及锂电池制造行业均已跻身世界先进行列,诞生出一批优秀的本土品牌企业,而工控自动化厂商也借着有利条件,活跃在这些新能源产业的第一线。
全球新能源汽车驶入快速道
3月初,工业和信息化部部长肖亚庆表示,我国新能源汽车产销量连续6年蝉联世界第一,累计销售550万辆。同时他也指出,近年来,国家相继发布了约60多项支持政策和举措,新能源汽车产业发展取得了积极成效,基础材料/零件、电机、电控、电池以及整车等各方面都取得了实质性突破,2020年新能源汽车增速达到了10.9%,并呈现持续增长的趋势。但另一方面,新能源汽车的发展还处于爬坡过坎的关键时期,新能源汽车市场竞争激烈,技术上、品质上、消费者的感受上也还有不少问题需要进一步解决。
“得电池者得天下”,根据中国化学与物理电源行业协会动力电池应用分会的统计分析,2020年中国新能源汽车动力锂离子电池装机量累计为63.3GWh,同比增长1.8%。从电池类型看,2020年三元动力电池装机量39.7GWh,占总装机量的62.7%;磷酸铁锂动力电池装机量23.2GWh,占总装机量的36.7%。智能化、网络化是电动汽车发展的大势所趋,越来越多功能要实现,电池能量密度不断提高是必然要求,一是要提升材料的技术水平,例如三元路线的高镍少钴(或无钴);二是要简化电池结构,例如比亚迪于2020年初推出的刀片电池,在安全性、续航能力上均实现了大幅跃升。
而从全球范围来看,现阶段各大车厂已经把汽车电动化的具体日程表明确了下来。戴姆勒集团计划到2022年推出超过10款纯电动汽车;大众集团将在今后5年间对混合动力、电动出行以及数字化领域投资600亿欧元,实现到2029年累计销售纯电动汽车2600万辆的长期目标;宝马计划到2025年推出25款混合动力车型和12款纯电动车型。丰田则宣布,将在2021年推出使用固态电池的新型电动汽车的原型车,丰田计划最初面向商业客户和地方政府销售约100辆这样的新能源汽车,2022年以后再面向普通消费者销售,这与日本政府到2030年代中期停售燃油车的方针相一致。
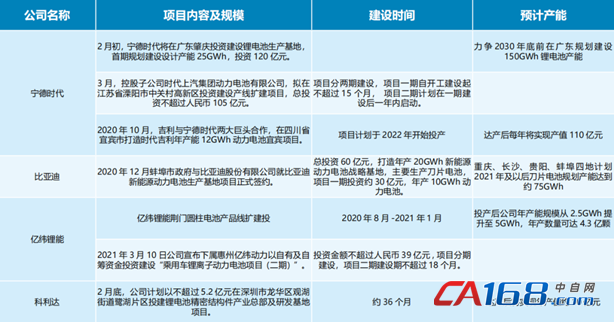
表12020-2021年国内锂电池产业链部分扩产情况(截至3月10日)
新能源汽车的三大件——电机、电控、电池,依然是目前技术上研发的重点,目前工控自动化领域厂商参与较多的是电控技术和锂电池制造设备的开发。作为变频驱动技术平台的一个重要的应用分支,新能源汽车市场电控技术的集成化发展可谓是一日千里,汇川技术、蓝海华腾、吉泰科等都是该领域中的佼佼者。
在锂电池制造设备的开发上,随着近一两年中国锂电池生产厂商(如宁德时代等)在全球新能源汽车产业链中的地位突显,也带动着整体产业掀起了一波扩产高潮,除了伺服与运动控制厂商积极投入其中之外,一些直驱技术厂商的身影也越来越多地出现在这一新兴领域中。
光伏制造跻身世界领先行列
经过近二十年的发展,中国已形成了完整的光伏产业链,技术水平和制造规模均处于世界前列:中国光伏累计装机量连续6年稳居世界第一,新增装机量连续8年保持全球首位,多晶硅产量连续10年位居全球第一,光伏组件生产量连续14年名列世界前茅。
根据中国光伏行业协会的报告显示,2020年,中国光伏新增装机规模为48.2GW,同比增幅超过60%,光伏累计装机规模为253GW。总体来看,2020年虽受疫情影响,但全球光伏市场仍保持了增长势头,这主要得益于中国光伏行业市场表现出的恢复性增长,据预测,2021年光伏将占据可再生能源增量市场的半壁江山,2021年中国光伏新增装机规模将达到55-65GW,“十四五”期间,国内年均光伏新增装机规模约为70-90GW(图2)。
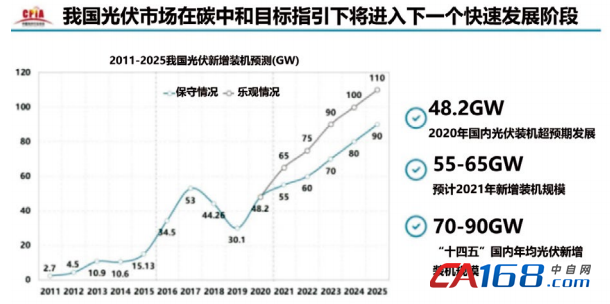
图2 2011-2025年中国光伏新增装机量统计及预测
(数据来源:中国光伏行业协会)
从产品供应链来看,近年来国内从上游的硅料,到中游的硅片、电池片,以及下游的组件等,整体都保持着稳定的增长率,尤其是组件出口量在总产量中的占比维持高位,充分显示出海外市场对光伏发电不断增长的需求趋势。2020年,中国多晶硅产量达39.2万吨,同比增长14.6%;硅片产量约161.3GW,同比增长19.7%;电池片产量为134.8GW,同比增长22.2%;组件产量达到124.6GW,同比增长26.4%。
进入2021年,从硅片、工艺优化以及电池结构等方面进行升级,进一步提升电池效率,是产业链中各重要厂商在技术开发上的主要方向。电池行业是光伏产业链中集中度最低的环节,但是也是整个光伏产业链里增效最明显的环节,目前该领域主流的电池技术以PERC为主,为了突破电池转换效率的“瓶颈”,一些厂商也在积极布建以HJT异质结电池技术为代表的新型电池生产路线。HJT不同于PERC电池,其对工艺和设备的要求更高,其中,无论是非晶硅镀膜设备(PECVD)、TCO镀膜设备(PVD&RPD),还是金属化制程设备(丝网印刷机),技术路线和竞争格局均尚未稳定,开发厂商的机遇与风险并存。
直驱技术在锂电池生产中崭露头角
新能源汽车动力锂电池的整个生产流程,大致上可以分为电极制作(前段)、电芯装配(中段)、后道处理(后段)三大过程工序(如图3所示)。前段设备(如涂布机、辊压机、分切机等)和中段设备(如制片机、模切机、卷绕机、叠片机等)是决定锂电池质量和性能的关键,因此对于生产设备的控制精度和稳定性要求较高。而锂电池后道生产设备,如化成、分容及检测、Pack组装设备等,则对于产线柔性化的要求更高,提高后段设备的自动化程度是关键。以往伺服系统应用较为普遍,但目前,直驱技术的应用优势在这一领域也开始崭露头角。
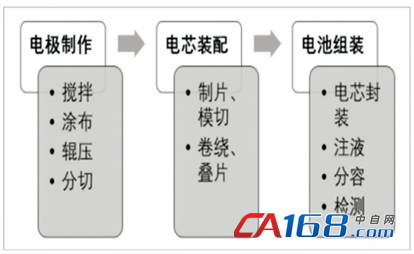
图3 锂电池制作工序流程图
前段设备涂布机环节,钢辊作为整个涂布机系统的主辊,起到稳定和传输作用,运行的平稳性直接影响到涂布的精度,涂布机钢辊的运动控制系统要求能够缩小误差值,缩短加速时间并实现位置锁定,提升极片的密度和精度,有效降低极片的次品率,此外,目前主流的涂布机一般的生产速度为60米/分钟,仍然无法满足锂电池厂商的生产需求。
为了帮助厂商解决应用难点,科尔摩根采用DDR马达替代之前减速机+伺服的方案,该DDR马达类似于一个伺服空心轴,通过压缩联轴器,DDR马达直接抱紧滚轴延伸轴,无机械背隙和柔性连接,直接带动钢辊高速转动。同时搭配科尔摩根AKD驱动器,缩短了产线的组装时间,减少了部件数量,提高了系统稳定性和精度,涂布机生产速度从原来的60米/分钟大幅提升到80米/分钟,提升了涂布环节的产能,充分满足了涂布机钢辊的性能要求,显著提升了涂布机的设备精度,帮助涂布机设备厂商增强了竞争力。另外,涂布机极片工艺的优化,也帮助锂电池厂商改善了生产效率和产品质量,大幅降低了生产成本。
在锂电池极片模切机上,传统模切机的停切控制张力机构通常采用普通伺服电机加丝杠的方式,通过控制动滑轮机构上下移动来控制张力,然而当速度接近1m/s时,丝杠噪音明显增大,润滑状况急剧恶化,所搭配的减速机的精度也会因为长时间的磨损而逐步丢失,不但令维护保养的成本增加,而且严重影响到产品的精度。为此,科尔摩根在这一工艺段因地制宜地使用适合筒类应用的CDDR模块化直驱电机取代丝杠传动,将负载直接耦合到电机上,无需减速机构,使得设备的整体速度一跃突破至45m/min,可在无需维护的情况下长期保证产品的精度。
另外,在锂电池顶盖激光焊接机方案中,针对轨迹焊接速度小、精度差、焊接良品率低等问题,科尔摩根运用DDL直线电机+AKD驱动器方案之后,可达到250mm/秒的正常生产速度,特别是满足了小圆角焊接稳定性所需要的较高的加速度要求,提高了生产效率,且位置偏差控制在±50微米以内,实现了高响应度、高精度的运动控制效果,提升了电池焊接的密封性,提高了良品率。
高动态转台提升光伏电池制造效率
在太阳能光伏硅片电池(PERC)的制造流程中,目前国产设备在加工效率、加工效果等方面与进口设备不相上下,且具备明显的成本优势,以单晶PERC电池制造为例,PECVD、扩散炉、清洗制绒、自动化、丝网印刷机等生产设备被用于多个主工艺之中。
太阳能光伏硅片丝网印刷机是电池片的重点工艺设备之一,直接影响到电池片的成品质量,属于光伏电池片设备的后道工序。主流的太阳能光伏硅片丝网印刷机多为转盘式(另外也有部分通过式丝网印刷机),采用四工位转台结构设计,依次进行拍照定位、网板移动与硅片对位、网框下降进行印刷、卸片这四道工序。由于在加工过程中,印刷的电极栅线必须要与扩散之前用磷浆印的栅线重合,因此要求丝网印刷机能够有精确度较高的定位系统,高精度是太阳能电池丝网印刷机发展的根本,也是未来新工艺开展的前提。
DD马达(力矩马达)等直驱技术有着输出力矩大的特点,可直接与转台负载连接,具有较高的定位精度,重复定位精度更稳定,因而这类大惯量的直驱电机非常适用于转盘式光伏电池丝网印刷机的应用场景,据了解,目前科尔摩根、上海奥茵绅等国内外厂商都在该领域已有了成熟的应用案例。此外,视觉系统及UVW平台细微环节都会对于印刷精度有较大的影响,两者配合后的定位精度达到±12.5μm以下,叠印才会有更好的效果。
“碳达峰”、“碳中和”,正在为中国社会与经济带来一次翻天覆地的变革,新能源产业的发展必然经历技术的不断更新迭代,未来还有很长的一段路要走。要实现“碳达峰”、“碳中和”的目标,同样需要包括直驱技术厂商在内的工控自动化行业的全力支持与配合,助力高端装备制造业的整机开发,让中国太阳能光伏、新能源汽车等新兴产业继续屹立于世界之巅。