在玻璃生产中,最显著的是产线首末端的上下片由人工或传统简易取放设备完成,未能实现自动化,这种人工操作流程不仅效率低下,且产品品质很难得到保障,无法实现产线的物料和数据的有机对接。因此,提升玻璃上下片环节的自动化水平,打通各产线环节的连贯性是实现数字化、自动化、智能化玻璃加工厂的首要技术难题。
川崎机器人深耕搬运、码垛应用领域多年,无论是小到几克重的零件还是几千克的大型产品,都能搬运自如。川崎机器人的全系列机械手均可满足各企业的需要和要求,并凭借卓越的技术和强大智能的机器人系统得到客户的一致认同与青睐。
鉴于市场需求和机器人技术的广泛应用,川崎“携手”凯盛,依托集团深耕建材行业数十年经验,结合玻璃制造工厂的工艺特点,开发出全自动玻璃智能化上片系统和智能化下片铺纸系统。其中,系统集成应用了川崎BX200L型号机器人、RS(机器人控制)系统、其他相应配套设备等。
与市面上的同类产品相比,此集成机器人技术已相当成熟。目前,集成机器人玻璃上下片系统已在集团内外多家企业,数十间工厂内成功应用,累计使用的机器人数量超过200台,并已完成玻璃抓取与堆垛关键技术的开发和验证。不仅如此,配置了川崎机器人系统的集成玻璃上下片系统还有着自动化水平高、效率和成品率高等优势。
堆垛成品率达99.9% 最快节拍7.5秒
在中空玻璃生产过程中,对于自动中空线及封胶后的成品中空玻璃下片工序,大部分工厂采用工人搬运或用手吸盘吊架人工操作下片。人工搬运中空玻璃容易将胶弄到工人身上,而且还会影响封胶效果,玻璃破损率高。吸盘吊架玻璃下片的形式,设备占用空间太大,不仅需要很大的活动范围,而且操作十分笨重,无法满足灵活运载不同厚度、重量的玻璃的需求。
集成机器人玻璃上下片系统中使用的BX200L、RS080N以及CX210L等川崎机器人打破了这一下片难题。川崎BX200L机器人坐落于产线两侧,当玻璃到达输送辊道定位停止后,机器人吸盘架通过提升机构升起,同时打开真空吸附玻璃板,最快抓取吸附节拍可达每片7.5秒,当玻璃高于辊道后旋转、提升和翻转机构一同运行,将玻璃运至符合堆码要求的相应堆码平台上,并根据平台上玻璃已放置的厚度自动调整高度,放下玻璃板后返回等待下一片玻璃。
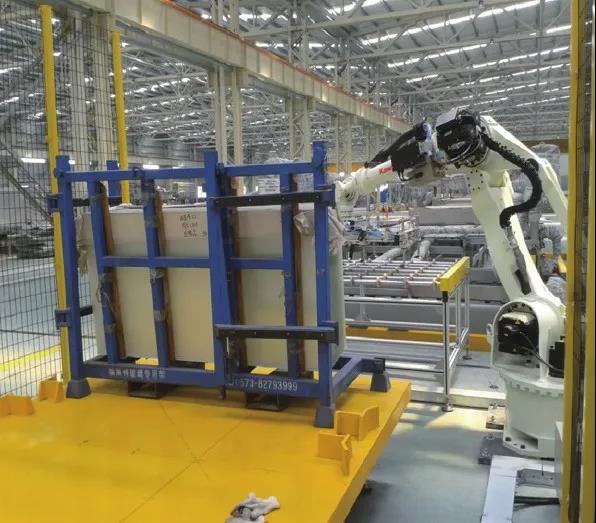
从运作过程中不难看出,川崎BX200L机器人的整个下片堆垛过程十分灵活、快速且占地小。据测试每台机器人相当于4名搬运堆垛员工,大大减少操作工人数量配置,提高生产线效率。而且,川崎机器人堆垛不仅快,还保质保量,成品率可达99.9%,大大领先于人工或传统简易设备。同时,机器人配置还可根据客户玻璃的规格和产能进行调整,最大运动半径达2597 mm,抓取玻璃尺寸为3000mm*2000mm,且重量可达80kg,可谓是一台机器满足多样化需求。
在目前的单条生产线中,川崎BX200L机器人最多已连线应用24台机器人完成玻璃的下片工艺,可见其适用性也能十分“强悍”。
产线自动化有机衔接 搬运损耗率降至为零
玻璃加工之前,需要将待加工玻璃从垛架上搬送至工作台,这种搬运过程即为上片。现在不少企业采用的上片方式是人力搬运,几名工人将玻璃搬运放置于模具中间的支撑杆上,通过人工控制信号按钮,设备缓慢地降低中间的支撑杆,并左右调整位置点。事实上,玻璃上片对定位精准度和稳定性的要求非常高,人力方式费时费力,精确度也难以保证。
集成机器人玻璃上下片系统可配置视觉系统实现玻璃状态监测,或配置传感器实现机器人智能寻边,大大提高了精准度,降低人力资源浪费。在川崎的视觉系统中,提供两种PC视觉软件程序,分别为K-VFinder和K-VAssist,它们共同处理图像,并将结果分发给多达八个机器人控制柜,自动化程度高。
此外,由川崎机器人加持的集成机器人玻璃上下片系统能够配合生产线上的输送系统实现全自动化连续生产。工序与工序之间的自动化连线,无疑大幅降低玻璃搬抬或转运的工作量,提高生产效率。
以外墙玻璃为例,外墙玻璃由四层钢化玻璃夹胶而成,表面涂银以达到抗辐射、隔热、保温等效果。人工搬动时,如果因为受力不均造成玻璃不平整,或因为呼气、手印造成银的氧化,整块玻璃就报废了,损耗率达到10%。全自动玻璃上下片系统的应用,使整个生产过程中避免了人与玻璃的直接接触,损耗率甚至可降至零。
再如光伏玻璃的生产过程,如采用人工下片包装方式极易造成镀膜钢化后的玻璃表面沾有手套印迹,这是国内外客户都不能接受的品质问题。使用全自动玻璃上下片系统,以真空吸盘代替人工搬运,有效解决了手套印迹问题,经济效益与社会效益双赢。
智能化控制和算法系统
智能化上片机器人系统中包含公司开发的具有独立知识产权的无痕抓手系统、智能自适应探板系统,自动更换玻璃架系统、自动诊断判断玻璃规格系统。一般的上片专机由于设计机械结构的局限性,无法避免取片过程中产生的玻璃线、面的划伤问题。利用机器人的柔性路径,以及智能化探测玻璃板面角度问题,实时只能调整取片抓手的角度;同时取片动作轻柔,且巧妙的利用物理原理破解玻璃板之间的真空吸附力,而不会造成面板伤痕。此系统应用在行业内非常先进,智能。
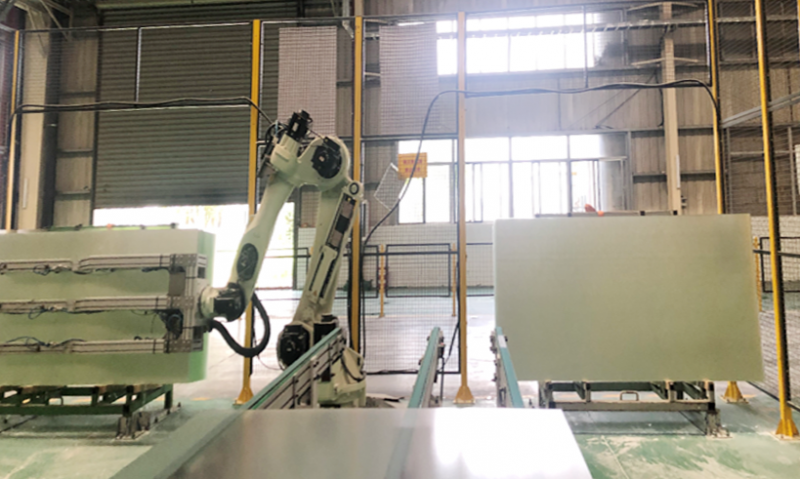
智能化上片机器人系统图
智能化下片铺纸系统,与铺纸系统和辊道输送系统配合,输送系统控制器通过通信把生产玻璃规格传递给机器人系统,机器人会根据规格尺寸计算出抓取位置,以及铺纸系统中的放置位置,智能化的适应输送系统的调整,以及铺纸系统的调整。
同时,机器人系统与视觉检测系统相结合,智能化的把有缺陷的产品择出来,归类处理,单独码垛,提高铺纸系统的良品产品处理效率。
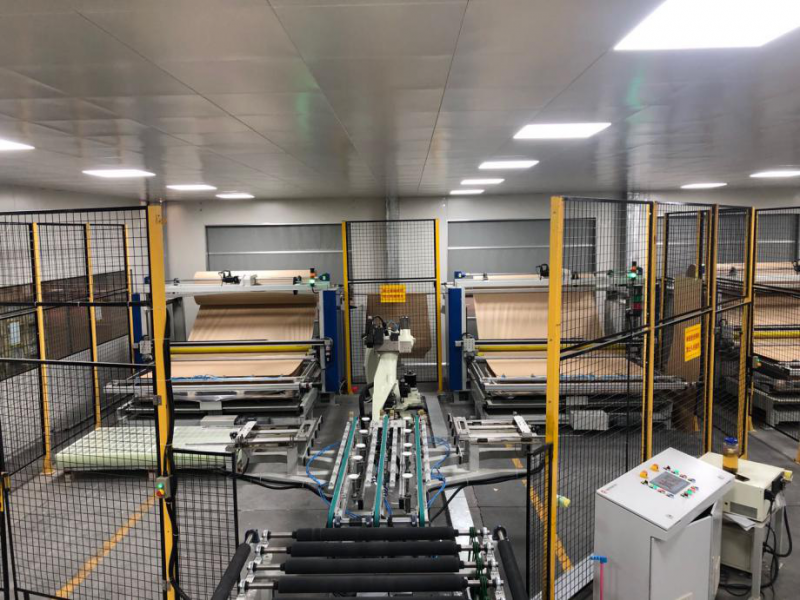
机器人下片铺纸系统图
结语
虽然我国已成为世界上规模最大的平板玻璃生产国,但高端市场依然被国外占据,特别是随着美国制造业逐步智能化,唯一的人工成本劣势也将逐渐被磨平。面对挑战,我国玻璃制造业需要的是高端技术的积累与运用,而非在中低端抢占微薄利润。
因此,打造全面智能化、自动化玻璃产线是大势所趋,是未来智能制造的重要装备,推进产业向中高端迈进的关键。作为大多使用人工的玻璃上下片工序亦是如此,实现产线连续性衔接,上下片环节的自动化、智能化水平升级迫在眉睫。川崎机器人助力玻璃深加工产业突围自动化困境,为智能制造树立信心。