工业4.0是以智能制造为主的第四次工业革命,将传统制造技术与互联网技术结合,通过信息化与自动化高度融合,实现智能化的生产制造。
在制造企业有IT(信息技术)和OT(运营技术)之分。
IT(Information Technology),即信息技术,是用于管理和处理信息所采用的各种技术总称,主要是应用计算机科学和通信技术来设计、开发、安装和实施信息系统及应用软件。
OT(Operational Technology),指操作技术,是工厂内的自动化控制系统。操作员为自动化控制系统提供支持,确保生产正常进行。
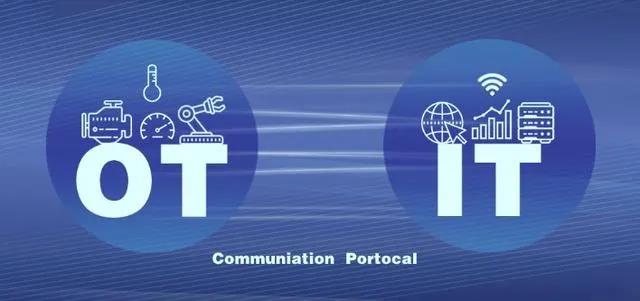
IT/OT融合加速(图片来源于网络)
随着新一轮工业革命的推进以及数字化时代的到来,制造业的智能化转型正在让现实与虚拟世界之间的界限变得越来越模糊,带有IP地址的网络设备正在快速大面积覆盖智能化工厂。当生产过程和信息合二为一,企业需要新的运营模式,要求IT和OT进一步深度融合,形成了一个贯穿整个制造企业的技术架构。
未来企业的运营核心是弹性决策,深度挖掘客户需求和生产规划,改善业务系统以及各部门之间的整体的信息流动,从而提升企业的运营水平,为企业创造价值。
得益于开放的系统架构和创新的软件应用,制造企业重构IT和OT部门,试图通过双方在同一个项目开发或者生产流程中彼此协作,让数据从设备层-控制层-信息层直至云端无缝对接,从而在输出中充分体现IT和OT融合的特性。比如PLC作为企业网络上的一个物理节点首先要是远程可建立连接的,除通过授权访问,更要求保证网络连接的安全性。
在这些IT与OT系统的集成中,最常见的是企业资源计划系统(ERP)、过程控制系统、制造执行系统(MES)、实验室信息系统、设备维护管理系统、数据采集与监控系统(SCADA)等之间的交互,从原材料到制成品,每个环节都需要使用OT数据来履行专门的职能。
然而,历来企业的信息技术(IT)团队和运营技术(OT)团队很大程度上是彼此独立工作的。
OT专业人员偏好使用PLC、DCS、RTU、HMI、SCADA,以及嵌入式计算技术。而IT 包括用于企业管理的硬件、软件、网络、通信技术以及存储、处理和向企业各个部门传输信息的系统。
在技术层面,IT与OT融合最大的困难在于:数据网络的传输接口与标准不统一,IT首先要能够访问OT端的数据,这就是现实中的难点。
在解决问题的工作和思维方式上OT和IT也往往不同。IT采用自顶而下的方法,惯于从总体需求出发,然后划分为若干的子部件,且针对子部件提出和开发解决方案。OT 人员习惯于自下而上的思路,从个别的部件出发构建复杂的系统。
不同的使命、文化、教育背景只造成了IT和OT两个组织截然不同的世界观,不熟悉彼此如何工作,缺乏系统组织等。IT和OT部门关系没有统一的指导方法,硬件、软件和操作环境等明显差异会造成部门之间的鸿沟。
作为制造企业非常重要的两个系统,IT与OT并没有融洽相处,“打成一片”;反而互不兼容,“打”成一片,让企业高层感到非常困惑。
为了从技术上面解决这些难题,很多信息化和自动化厂商开始发力,打通各环节壁垒,实现数据和信息的统一协调。
IT领域厂商在不断向OT领域渗透,利用其自身掌握的先进技术以及广阔的市场阵地,紧盯OT领域的“互联、互通、互享”需求,推出带有明显OT特征的产品和技术。如对于现场总线、安全网关甚至人机等设备。
从OT领域生产厂商角度看,传统工业自动化公司纷纷延伸其产品的IT能力,包括联合软件公司拓展的软件实力。也有一些自动化公司部署基础的IoT集成、Web 技术的融合方面的产品与技术,期望通过搭建软硬件平台帮助其用户快速实现数据互联。
从IT和OT从业人员来看,可以从以下三个方面改善两个部门之间的隔阂:
(1)让团队对OT业务的逻辑进行量化和标准化,业务场景的量化是一个很大的难点。
(2)数据完整和全面性的体现,在于工业现场如何把OT的数据转化为IT的信息。
(3)改造整个智能制造,转变工程师思维方式和改变技能。培养工业自动化、运营技术、信息三方面的融合人才,以人才赋能OT,打造现代化、智能化的OT团队,推动制造业的升级改造。
OT与IT融合必然创建提质增效的结果,赋予工厂管理者监控运行和过程的能力大为增强,甚至可以预测到可能发生的任何意想不到的事件,未雨绸缪。IT与OT深度融合会加速生产节拍或速度、使能源和时间的消耗最小化,以及降低监控资产的成本。但将两个本质不同的组织以及技术结合起来并非易事,仍然需要克服很多障碍。