01
企业简介
郑州宇通客车股份有限公司(简称“宇通客车”)是一家集客车产品研发、制造与销售为一体的大型现代化制造企业,目前公司日投产量最高达430台,年生产能力达70000台以上。主厂区位于河南省郑州市宇通工业园,占地面积1700亩,2012年新建成投产的新能源厂区占地2000余亩,建筑面积达60万平方米,拥有底盘车架电泳、车身电泳、机器人喷涂等国际先进的客车电泳涂装生产线。
宇通客车于1997年在上海证券交易所上市(证券代码600066),是国内客车行业第一家上市公司。公司主要经济指标连续十余年快速增长,并连续十余年获得中国工商银行AAA级信用等级。2018年,客车产品实现销售60,868辆,其中销售新能源客车24,748辆,实现营收317.46亿元,销售业绩在行业继续位列第一,公司人数超过2万人。
公司已形成了5米至25米,覆盖公路客运、旅游、公交、团体、校车、专用客车等各个细分市场,包括普档、中档、高档等各个档次,国内75个产品系列,海外69个产品系列的完整产品链。
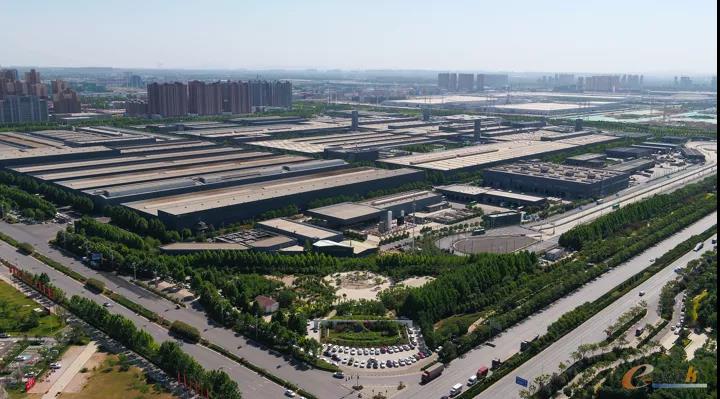
图1宇通新能源厂区俯瞰全景
02
企业智能制造现状
作为我国客车行业的领头羊,宇通客车对工业化、信息化有清晰的前瞻性认识,高度重视先进技术的应用,同时根据国家政策及企业发展,将智能制造纳入公司战略,积极探索企业智能制造在企业的应用,支撑企业的业务目标达成。近几年宇通平均每年投入上亿元支持信息化建设和生产装备改造升级。截止目前宇通在工业化和信息化等方面建设情况如下:
在工业化建设方面:
宇通拥有国内领先的桥壳焊缝机器人自动焊接线,其领先的半轴套管摩擦焊接工艺实现行业领先,拥有关键零部件的激光切割、机器人自动化组焊工艺,实现了大总成(如侧围骨架)模块化设计、柔性工装+自动化焊接,实现了适合客车的独创的蒙皮复合冲压、辊压工艺,这些工作有效保证焊缝的高质量,提升了产品质量和生产效率。截止目前宇通累计已投入机器人超过350台,形成了智能弧焊机器人设备、集成除尘降噪设备、重型焊接变位机设备、数控合装胎设备、先进的电泳线、涂装机器人喷涂系统、板材激光下料系统、板材高精度折弯系统、型材激光及锯切下料设备等先进的智能化装备和加工系统;
在信息化建设方面:
从1994年开始,宇通先后实施建成以宇通先后实施建立CAD、ERP、PDM、EIP、CRM、BI、CAPP、LES、MES、HR、售后服务网、供应商门户、海外业务管理、质量信息管理、销售配置器、一卡通等系统,全面集成了公司技术、生产、供应、销售、售后、财务、质检、仓储、办公、人事、后勤等业务,对公司的业务管理的科学化、规范化提升起到了很好的促进作用,持续推动公司各项业务的改进和提升。
数据驱动业务改进创新方面:
公司通过企业数据治理,搭建企业数据标准和架构,使数据成为企业核心资产,基于BI平台,实现数据的深度开发利用,支撑公司高效运营。
信息技术引领模式创新方面:
公司当前正同步进行云平台的建设,目前已完成Iass、Pass两个层级平台搭建并已完全成熟应用;大数据平台按照内部运营、产品两条线试点应用;车联网技术已深度融入产品,支撑车辆的远程运维和维护保养等。公司积极跟踪先进的信息技术和工业技术,通过持续的对标学习和创新实践,推动公司两化深度融合。
鉴于宇通客车在工业化、信息化方面不断创新实践和取得的成绩,2012年宇通客车被河南省科技厅认定为“数字化企业试点单位”,同年被工业和信息化部认定为“国家级信息化和工业化深度融合示范企业”。2016年宇通客车获得国家“客车智能制造试点示范”。
03
项目详细情况
1.项目背景介绍
在客车领域,随着国内客车行业的发展,我国已经成为世界最大的客车生产国。与国际领先企业相比中国客车企业在产品多样性、适应性及人工成本方面具备一定优势,但在产品品质、生产效率方面仍存在一定差距。究其原因,国外客车企业(比如德国奔驰)只生产少数几种车型和配置,装备自动化、智能化程度比较高。而中国客车主要是定制生产模式,车型种类及配置要求多,同时生产过程采用大量的人工和简单设备加工。随着人工成本的不断增加,市场对质量要求的不断提高,原有竞争优势不再明显,竞争压力不断增大,国内客车行业由劳动密集型向自动化、智能化制造的转型迫在眉睫。
宇通客车在探索智能化工厂建设方面,始终走在行业的前列。在软件体系建设方面,早在2002年宇通就率先搭建了ERP系统,构建了包括客户关系管理系统CRM、制造执行系统MES、物流执行系统LES、供应商门户SRM、产品数据管理系统PDM等系统,形成支持从客户需求到产品交付全生命周期的IT系统架构。通过销售配置器,实现与客户间深度交互选型,ERP系统自动生成物料采购计划、物流计划、生产计划、质量监控技术。PLM方面进行CAX的扩展应用,完善3D工具和应用模板,完善PDM系统,升级工艺管理系统,形成适合客车的新的CAPP系统并与PDM进行集成。ERP将计划传递给MES系统,CAPP将工艺流程、参数等信息传递给MES,MES按各计划实现物流控制与管理、生产成本控制与管理、数据统计和生产调度及质量控制。
在硬件体系建设方面,宇通已逐步建立企业级光纤环网、车间级通讯网络,实现全面信息互联。同时通过新的关键技术装备开发应用以及部分离散设备的智能化升级,并建立统一的数据采集平台,将设备硬件与信息系统连接,实现数据互联互通。
宇通客车将通过智能工厂建设,提升智能化生产水平,带动公司信息化转型发展、创新发展,从而实现制造成本的降低和资源利用率的提升,支撑企业实现工业化转型。
2.项目实施与应用情况详细介绍
宇通智能化工厂建设主要包含:建立工业网络基础以及网络安全管控体系,实现设备的联网和数据采集,同时提高制造装备的智能化水平,重点对较薄弱环节的设备、物流体系进行智能化建设和升级,并在生产管理层搭建MES系统,实现整体生产过程的透明化管控。
具体实施任务如下:
建设工业网络和工业互联网平台,为智能工厂建设提供网络基础,并实现设备的互联互通,采集设备数据信息,支撑生产管控,同时建立系统的网络安全管控方案,为整体运行提供安全保障。
智能生产系统建设:通过集中建设和升级一批智能化生产装备群,包含:白车身分总成智能加工装备群建设;白车身总成智能制造体系建设;客车涂装智能化柔性制造体系建设;客车总装数字化加工装备建设。
MES系统建设:建立车间级MES系统,与上述智能化设备群集成,构建具备生产组织、质量监控、设备监控、物料调度等功能的生产执行控制系统,并实现与ERP、PLM等现有系统无缝数据交换。
2.1工业网络建设及设备的联网和数据采集
1)工业网络建设
①网络架构设计
采用核心层、汇聚层、接入层三层以太网构架方式。汇聚层作为网络路由和交换的分界层,汇聚层与核心层进行Layer3连接,与接入层进行Layer2连接。
核心网络设备采用两台同规格的设备进行部署,两台设备实现冗余互备,单台设备故障不影响整体核心设备运行。随业务或用户的不断增加,核心及骨干设备的交换能力和容量可以进行线性增长,实现灵活的扩展。
核心层网络设备与汇聚层设备设计为万兆(10G)带宽;汇聚层设备与接入层以及接入层与终端设备设计为千兆带宽。
网络核心交换机支持未来异地数据中心在应用服务层面的快速切换,单个数据中心应用故障时,用户可以不间断对系统进行访问。
②布线设计
核心至汇聚层网络设备之间部署双链路光纤连接,实现负载均衡及单挑链路失效时的自动快速切换,保证整个核心网络的高可靠性。
园区内部的管网,设计为在各个建筑可达,满足后续业务扩展时网络可以快速部署。
在办公区域内,对所有房间隔段均部署信息点,在房间功能发生变化时网络可以快速联通。
园区内骨干网(核心至汇聚层)管网采用双链路冗余设计,两条链路走不同路径,线缆采用十二芯光缆布线;汇聚至接入层采用八芯光缆布线;接入层至桌面终端采用六类双绞线布线,接入层至生产车间现场采用六类屏蔽双绞线布线设计。
对布线系统的线缆,及线缆经过的各种配线架、面板等进行标签标记,可以快速的识别线缆的走向和功能,方便进行后续的维护。
③信息集成情况
随着宇通信息化建设的日渐深入,各应用系统之间的数据交换越来越复杂,数据传递的有效性和可靠性问题成为迫切需要解决的问题。在此背景下,宇通按照SOA理念搭建企业服务总线,并用企业服务总线方法支持宇通各信息系统的系统整合工作。
通过企业服务总线项目的实施,宇通搭建了完善的企业级的企业服务总线系统,以支撑宇通未来所有应用系统的数据交换。该系统的建设思路为将传统的点对点连接,更换为松耦合的总线结构,将业务逻辑和应用逻辑、数据逻辑等分离开,提供一个满足企业的应用集成和信息调解需求的解决方案。
借助企业服务总线的集成能力,梳理出来宇通客车的系统集成规范,对系统集成的技术方案、工作流程、工作模板都形成了标准,为后续的系统集成工作提供了指导性意见。
企业服务总线项目建设中涉及的的集成工作,所有系统接口纳入企业服务总线进行分类,达到了接口可视化、规范管理,为后期的接口重用奠定了良好的基础。
2)工业设备联网及数据采集
宇通客车通过建设工业物联网平台(架构图如下),实现了工业设备的联网数据采集、监控以及分析等功能,截止目前宇通生产现场已实现核心设备的联网和数据采集,包含焊接机器人、激光切割机、加注类设备、扭力扳手等设备,基于设备实施信息的采集,对关键加工质量、设备利用率、能耗、设备加工工艺参数控制等进行综合管控。具体宇通工业物联网平台主要分为如下几个层面:
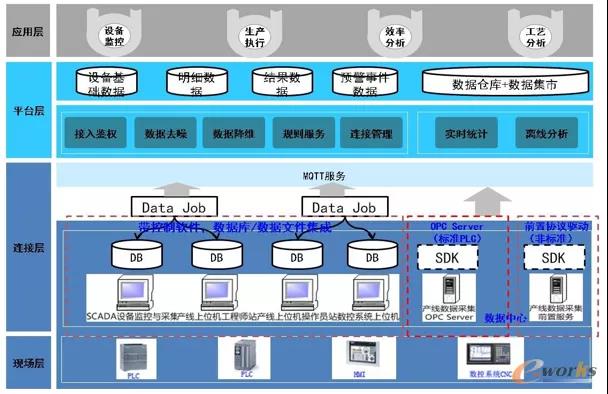
图2工业物联网平台架构
连接层:连接层主要负责将数据采集到平台层,根据现场情况,连接层主要由3种底层采集方法,第一种是针对标准PLC利用组态软件直连采集底层PLC控制器的寄存器数据并转发到云平台,部分设备需要进行网口改造,以方便组态软件采集;第二种是针对工控软件开发数据库或数据文件采集驱动实现采集,并将结果转发到平台层;第三种则是非标准部分(如自由协议),这种需要通过自定义编写通信协议的方式对设备进行通信;三种方式最终通过MQTT服务将数据转发至平台层。
平台层:数据通过MQTT服务转到平台后,云平台根据数据类型进行分别处理。数据主要包含三种。第一种是设备状态信息,设备状态信息主要包括设备的通信状态和运行状态,通信状态可以检测设备是否在线,运行状态可以检测设备的运行,停止,报警情况;工艺过程数据主要包括工艺在进行的过程中产生的实时变化数据,如温度,压力,转速等;工艺结果数据则是设备在进行某一工序后得到的结果,通过一个工序后只有若干条结果。各类数据通过规则服务来判断是否触发某些自定义规则来进行实时预警或后续处理。所有采集数据保存到分布式数据库。
应用层:应用层主要包含看板系统和数据服务两部分。看板系统主要包括设备看板和生产过程追溯,设备看板主要针对设备的运行状态的实时监控和统计,生产过程追溯,即可通过内部车辆生产编码追溯其在各设备的生产工艺数据;数据服务主要是为其他应用系统提供数据支持,包括实时设备、工艺数据及分析型数据,比如说MES,ERP等系统。
3)信息安全保障情况
宇通信息安全体系构建以信息安全技术为支撑、信息安全管理为抓手的体系架构,核心理念是对信息资产的保护。
宇通信息安全组织分为管理层和执行层两个层面,其中管理层由公司信息安全管理委员会、信息安全管理小组、体系信息安全专员和部门信息安全管理员构成,负责公司信息安全的各项工作。
宇通已制定信息安全管理程序,涵盖资产、人员、终端、系统、审计五大领域。
宇通信息安全技术体系已实施部署安全工具涵盖终端、网络、系统三个层面。安全工具包括:
终端安全工具:防病毒、文档加密、数据防泄漏、外设管控、数据备份、补丁管理、域管理;
网络安全工具:防火墙、入侵防御、VPN、网络准入、上网行为、网站防火墙;
系统安全工具:堡垒机、漏洞扫描。
2.2智能生产系统建设
在关键智能装备应用方面,宇通智能工厂项目围绕白车身分总成、白车身总成、涂装、总装制造体系建设等主线进行开展,通过联合开发或自开发,取得了全自动数控型材直切锯系统、型材三维激光切割系统、平板数控激光切割机自动上下料系统、涂装柔性化物流系统、机器人集群管理系统、数控合装胎管理系统等多项核心技术装备突破。详细建设情况如下:
1)白车身分总成数字化加工装备群建设
在白车身分总成数字化加工装备群建设方面,项目重点围绕钣金加工装备群建设、型材加工装备群建设以及机器人自动化焊接群建设内容开展,有效支撑了材料利用率、单车工时指标的达成,并有效保证了产品精细度及产品一致性,从而提升了产品下线一次交接通过率。
①钣金加工装备群建设:为提升钣金加工的效率和质量,项目开发和推广了包括平面激光切割自动上下料系统、冲剪复合机柔性加工生产线、三维激光切割系统、冲床自动上下料系统、折弯机器人系统、检修口自动加工生产线、直角剪下料自动分选系统等,通过以上工艺的开发和推广,实现了设备集中智能排版、数据的远程投放、程序的自动执行、报表的自动生成,在客车钣金加工方面实现重要突破,部分技术已达到国内、行业先进水平,应用效果如下:
a)平面激光切割机及自动上下料系统:平面激光切割自动上下料系统开发的智能料库和自动上下料输送系统实现了“一拖二”、“一拖三”的模式,实现了不同规格原材料的快速切换,解决了钣金行业多品种、小批量加工过程中原材料切换效率低的问题,目前该设备运行稳定、可靠,技术成熟度高。与国外同类设备相比,采购成本大幅降低,具有重要示范作用,可在钣金行业快速推广;
b)冲剪复合机柔性加工生产线:该生产线实现了转塔冲床与直角剪设备相结合,柔性化程度高。对于孔类加工使用模具冲裁,外形切割使用两个互成90°的剪刀裁切,剪切间隙根据材料厚度自动智能调节,可实现半剪和全剪功能,比数控冲床以冲代剪的方式效率大幅提高,并解决了冲切过程产生的接刀痕问题,加工能力达到国内先进水平。
c)三维激光切割系统:该系统开创了模具冲压与激光切边工艺相结合的生产新模式,通过快速切换程序和夹具,即可满足不同产品。高度的柔性化,解决了客车行业中多品种、小批量定制化生产投入全序冲压模具成本高的问题。
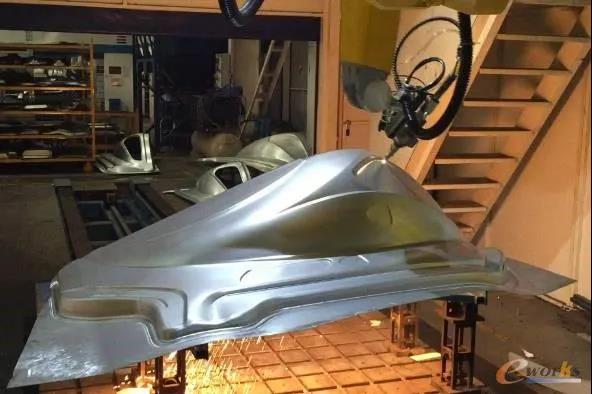
图3三维激光切割机
②型材加工装备群建设
项目开发和引进了包括型材三维激光切割机、数控直切锯床、型材弯弧成型设备、数控伺服双头钻床、数控双头切剪复合机、型材精度检测仪等多台套设备,不仅提升了型材加工质量精度,还带动了国产技术的创新和突破,降低了设备采购成本的同时实现了关键技术和设备的国产化,应用效果如下:
a)型材三维激光切管系统:型材三维激光切管系统是集激光切割、精密机械、数控技术等技术于一体的高柔性化加工装备,该设备的加工质量、效率达到国内领先水平。开发的电泳孔自动识别技术、参数化建模技术、智能排版套料切割技术、超长切口切割轨迹算法等都超过国外同类设备,解决了多项行业技术难题。设备采购成本远低于进口设备,实现了国产全自动激光切管机的产业化。
b)全自动数控型材直切锯系统:该系统开发的套料软件和排版逻辑,可批量加工也可混合排产,实现柔性化加工;开发的动态进给锯切模式和零料头锯切功能,降低了加工节拍、提高了材料利用率。实现了型材自动上料、自动锯切、自动出料,生产过程无需人工干预,同时解决了进口设备不适合小批量、多批次加工的问题。
c)数控双头切剪复合系统:数控双头剪切复合系统具备锯切、钻孔复合加工能力,可根据工件长度和角度自动调整,通过参数化编程,适应不同长度、不同角度内产品的加工,,两个锯切头分别独立控制,可实现不对称工件锯切、钻孔一体化加工,技术水平国内领先,客车行业首次突破。
③自动化焊接建设
通过工作站的自主集成和柔性化夹具的研发,焊缝一次合格率达到95%。在多品种、小批量产品柔性自动焊接加工模式上实现突破,应用效果如下:
a)后高地板机器人工作站:项目开发了双机器人联动控制、柔性伺服夹具系统,实现了客车行业多品种、小批量产品柔性自动焊接的突破;通过结构模块化整合,将产品由136种整合成2种,依据整合后的产品,开发出柔性伺服夹具,实现无级切换,应用磁性定位块实现定位、夹紧,可满足上千种产品加工。通过离线仿真模拟分析计算,合理分配焊接区域,实现两台机器人联动作业。
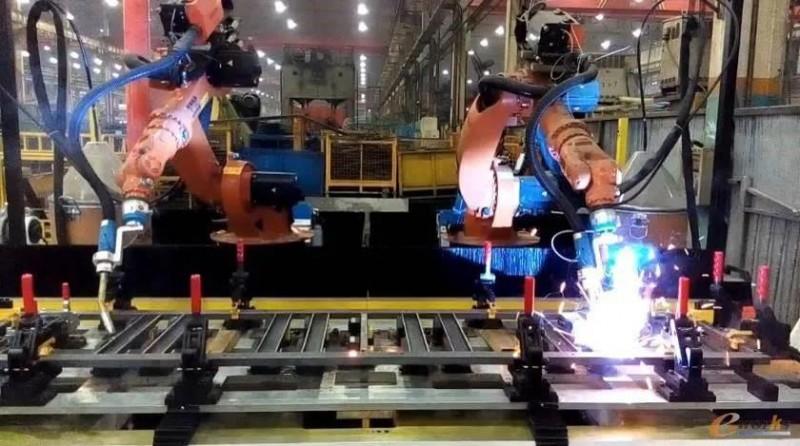
图4机器人工作站
b)空调固定件机器人工作站:该项目开发了免示教工艺和柔性伺服夹具,实现了多品种、小批量产品的柔性自动焊接,在客车分总成自动化焊接免示教技术上实现突破。开发的伺服夹具,可自动切换、自动复位、自动夹紧,可进行无级切换,满足上千多种产品共夹具生产,解决夹具频繁切换和转运的问题。免示教工艺行业首创,人工使用条码枪扫描加工任务单,夹具根据PLC信号自动调整,系统自动计算相对基准轨迹的偏移量,机器人根据偏移量生成新的运动轨迹,实现产品免示教工艺。无需人工针对每个物料进行编程、示教,实现了多品种、小批量产品的柔性自动焊接工艺免人工示教的突破。
2)白车身总成数字化制造体系建设
白车身总成数字化制造系统基于宇通分层分类焊装自动化、智能化的实施策略,以侧围机器人焊接工作站、前后围自动化焊接作业岛、数控化合装胎等三个代表项目分层开展。侧围机器人焊接工作站是针对大型总成自动化焊接的攻关项目,该项目的投入应用为探索大型总成智能化焊接铺平技术道路。前后围焊接作业岛项目是针对前后围总成和模块化分段中型总成的双机器人双工位工作站试点,项目投入使用后收到较好经济效益和示范效果,现已推广应用。数控化合装胎项目是针对白车身总成精度提升和生产效率提升的装备更新和改造项目,通过硬件改造提升了关键装备定位精度,同时降低设备故障率,通过合装胎综合管理监控系统试点应用,实现了合装工艺数据的云管理。
①侧围机器人焊接工作站:侧围机器人焊接工作站集成了弧焊机器人集群系统、柔性工装系统、移载变位机系统、工装切换系统、工装库系统、除尘系统等6大系统,实现了机器人集群同步焊接、激光视觉焊缝识别、焊接参数智能选择、工装自动切换、工装库自动存储、重型移载变位机精确位控。通过多种扫描及寻位技术综合运用,同时配合多焊种焊接参数专家库,保证了焊接合格率目标达成。
②前后围自动化焊接作业岛:前后围自动化焊接作业岛项目按照低成本、通用化的规划策略,工作站系统自主集成,先后自制4套中型焊接工装,累计生产一千多台套前后围总成;实现了设备选型标准化、工装接口通用化、机器人编程模块化。
前后围自动化焊接作业岛采用双机器人+双翻转变位机配置,结合通用化高精度夹具的应用,保证焊接总成尺寸精度;此作业岛作为中型工作站的范本,在车身总成焊装领域具有广泛的应用前景。
③数控化合装胎:通过数控化合装胎软硬件升级改造,试点应用了合装胎综合管理监控系统,实现6台合装胎设备联网和后台管理。数控化合装胎通过大量的伺服驱动装置实现定位机构参数化快速切换,有效支撑产能提升和多车型混线生产需求。搭建两级合装胎综合管理监控系统,在合装胎工位设置设备级服务器机台(II级)进行数据的收集、运算比对及交互;通过公司内部网络搭建管理监控平台(I级),实现合装工艺参数数据的云管理。
3)涂装智能化柔性制造体系建设
涂装智能化柔性制造体系建设主要从生产管理系统、颜色快换等方面进行建设和优化。经过各分项目建设实施,提升了涂装车间车辆的转运效率、生产效率和信息化管理能力,实现降本增效的目的。
①客车涂装生产管理系统:对不同单元的自动化设备与系统进行整合,互联互通,结合客车生产管理的特点开发了适合客车涂装生产管理的系统(B-PMS,Bus-ProductionManagementSystem),系统构架包含:设备管理系统、质量管理系统、计划管理系统、能源管理系统;
a)设备管理系统:设备管理系统突出对现场关键设备、重要设备目视化管理和预防性维护。通过目视化的人机界面,提升响应及时性,改善现场响应相对慢、设备问题点查找慢的问题;通过预防性维护系统的建立,解决预防性维护周期与实际设备运行周期脱节问题,从而提升设备利用率。
b)质量管理系统:质量管理系统突出对关键过程工艺参数(比如:温湿度、烘烤参数等)的管理与监控。通过对过程参数的统计,可根据车工号进行过程质量参数
c)计划管理系统:该系统以涂装预排计划为输入,实时输出预排计划的实际执行状态,可对计划异常进行提前预警提醒,提升现场生产调度效率。
d)能源管理系统:本项目实现了对能源介质使用参数的采集以及关键高能耗设备状态的实时监控。通过信息化平台关注能源使用趋势,统计设备利用率,呈现能源使用情况。通过能耗状态的透明化、信息化管理,达到节能降耗的目的。
②颜色快换系统的升级:重点解决了客车颜色定制化导致的油漆浪费问题。通过液位控制与pig(一种推动管道中油漆的珠子)连锁功能的改良,控制pig的作用方式,当罐体油漆处于一定液位时,第二颗pig主动发射推动管道的油漆,减少管道油漆的填充量。此种方式一方面解决单台订单、少量订单喷涂经济性的问题,同时可以实现按需调漆,每个面漆颜色每次的填充量节约3.5L以上。
4)总装数字化加工装备建设
在总装数字化加工装备建设方面,通过采用自动智能装配设备和检测设备提升产品质量。通过管路气密性保压检测设备和车轮拧紧机等关键力矩在线检测设备,实现在线检测、诊断和预警,提升产品品质,并存储到数据库。通过物料的空中及地面自动化输送,大件助力装配,分装自动流水线及智能数控加工中心作业,解决物流差、生产效率低、员工作业劳动强度大等问题,支撑高质量、高效率、低成本、快交付的目标达成。
①全自动尼龙管下料机:行业首创,通过程序控制实现一套设备满足不同外径、不同颜色、不同长度的尼龙管定长剪切下料作业,管路的测量、拉料、剪切、管路标记和管路分配均为自动化作业。通过激光打码工艺,对尼龙管下料管路进行标记,取消管路粘贴标识工作,并有效解决低温(冬季)时尼龙管材质变硬导致的剪切崩口问题。
②车轮总成动平衡自动检测设备:制定不同轮辋共线生产方案,采用高精度工业用立式自动平衡机取代原有的卧式平衡机,自动平衡机和车轮分装线自动连接,有效检测车轮剩余不平衡量,保证平衡修正后车轮剩余不平衡量符合要求,有效防止因车轮动平衡不准导致的车辆发抖故障。车轮平衡检测线采用自动上下料、自动检测不平衡量取代人工推车轮及人工安装夹具作业,大幅提升效率并降低了操作工的劳动强度。
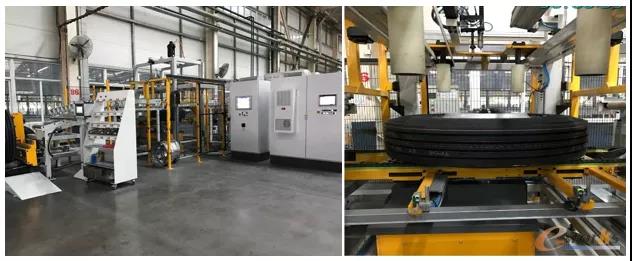
图5轮胎动平衡检测
③油液品集中供给自动输送系统:车间外建设集中供液站包含补液系统、储存灌、输送系统、控制系统、排污系统、安全系统等,涉及总装和底盘5个车间,柴油、防冻液、机油、齿轮油、制动液等11种油品,通过管道自动输送至各使用车间线边,线边加注点配备64台自动加注设备,采用物联网信息化管理(自动补液、加注数据联网管理、故障自动报警等),能实时监控系统运行状态(油量统计查询、故障报警点显示等)。实现油液品输送自动化,无需物流车辆进入车间,提升了车间内物流通畅性和效率,解决了传统液体加注工艺存在的人工搬运劳动强度大问题。使油液品无需线边存储,提高生产安全。
④玻璃自动涂胶机器人:玻璃自动涂胶机器人,包括机器人本体、玻璃夹具、搬运工装等。人工将玻璃放到指定位置,机器人自动吸取玻璃定位、自动完成涂胶,提高了涂胶的一致性和工艺质量。设备柔性化设计,能满足上百种玻璃的自动涂胶,玻璃涂胶实现自动化,同时替代人工作业降低劳动强度,员工基本不接触化工胶体,减少化工危害。
2.3MES系统搭建
宇通将MES系统定位于订单计划层和现场自动化系统之间的执行层,主要负责车间生产管理和调度执行。MES系统将集成计划排产、生产追踪、物料管理、质量控制等功能,同时为生产部门、质检部门、工艺部门、物流部门等提供车间管理信息服务。宇通根据企业实际情况,整体规划MES系统架构,计划、质量、物流等功能模块按照不同项目进行实施。通过MES与其它系统系统集成实现业务流程和数据打通。项目实施后,实现计划和生产整体协同,有效支撑生产节拍降低和生产过程质量提升。
1)计划排产管理
通过生产计划能力提升项目实施,建立IPS(IntergratePlanSystem)系统。使用价值流分析方法,完成半成品、焊装、涂装、车架焊接、底盘装配、承装、分装、线下全工序作业计划覆盖、打通及编制,能够有效指导一线员工生产。通过排产系统自主开发,实现以订单中心合装计划为输入的全工序作业计划系统编排,支撑物流准时配送。计划编排合理性、效率显著提升;
从作业效率、生产模式、物流模式等方面入手,优化排产逻辑,保证计划执行。通过计划指导生产,生产触发改善,改善修正参数,参数固化系统。
2)质量管理
通过QIS(QualityInformationSystem)项目实施,规范了各环节失效模式语言和检验标准,搭建了质量数据收集、分析和改进的平台,实现质量管理业务IT化。通过平台提高数据质量、优化管理方式、提升质量管理能力,实现自主管理和闭环管理,支持公司质量管理业务指标的达成。在质量改进、外购件检验、报表分析方面应用效果如下:
在产品设计、生产及交付、市场等环节基于PDCA方式实现质量问题闭环管理,监控质量改进过程和效果验证。
实现质量数据的多维度综合统计分析,分析结果准确性大幅提升,数据统计效率提升90%。通过报表监控发现主要问题,基于问题形成改善专项,支撑产品下线一次交接通过率提升。
3)物流管理
按照物料PFEP(PlanForEveryPart)规划、物流布局规划、新配送模式等思路实施LES(LogisticsExecutionSystem)项目,建立物流统一配送平台,实现了零件按时、按经济批量配送至线边,提升了物料配送及时率,降低了单车厂内物流配送成本。
根据物料不同特性规划出适用于宇通的JIT(JustInTime)、JIS(JustInSequence)主要物流配送模式,已在承装、底盘、焊装车间完成推广应用。
LES项目实施完成后,整体效果如下:
a)配送需求由手工整理变为系统自动计算,配送时间计算更为准确;简化直送物料需求传递方式,方便供应商操作;
b)物流路径单向循环规划,减少车辆堵塞,提升投料效率;
c)拉动订单中心将生产计划从原来的锁定T+1变为T+3,减少计划变动引起的后端效率浪费;
d)焊装、底盘、承装车间引入乘用车物料配送模式,实现了物料准时配送,支撑生产效率提升。
4)过程监控管理
生产异常信息快速录入,异常闭环管理流程固化到系统中,按照异常类别和等级逐层升级处理,保证生产异常得到及时解决,提升生产过程顺畅程度。现场质量问题通过移动终端实现及时、便捷录入,质量问题得以快速处理,支撑车辆下线一次交接通过率的提升。
①设备监控管理
目前正在建立全厂统一的设备数据采集平台,通过平台实现关键生产设备、车辆进度的数据采集,并分析设备使用情况、运行状态、工艺稳定性,支撑了设备综合利用率的提升。
②生产追踪管理
通过UWB技术实现车辆生产进度的实时跟踪,提高进度信息的准确性。根据车辆进度显示当前工位所需要的工艺卡、图纸、作业计划、历史质量问题等信息,规范员工现场操作,减少过程装配异常,提升产品下线一次交接通过率。
2.4智能工厂建设难点及建议
1)以“四化”为核心,逐步实现生产智能化
客车生产各环节自动化、智能化程度差距很大,且难易程度不一致。针对该问题,宇通以精益化、标准化、自动化、信息化“四化”为核心进行生产作业改善。通过对每一个工艺环节进行分析,逐点、线、面进行深入,然后逐步推进关键工序的自动化建设,总体围绕先试点后推广的原则,同时结合信息化的推广应用,实现智能工厂建设的逐步推进。
2)快速建立智能装备通讯协议、标准
通过宇通自身智能工厂的推进和过程对标调研发现,当前大多企业智能制造的推进是通过对现有工厂、生产线的改造开展实施的。在推进过程中一方面需要对当前的设备和系统进行联网和集成,另一方面新增采购相应的智能装备,企业对智能装备需求越来越大,但当前面临着设备与设备间的通讯协议缺失、通讯标准不统一等问题,造成智能制造推进难度加大。因此,企业应快速建立智能装备的通讯协议及标准,从而为设备与设备之间、系统与系统之间的互联互通、数据流动奠定基础。
04
取得收益
1)经济效益和业务支撑
随着智能工厂的建设,将进一步发挥宇通客车的整体优势,优化资源配置,提高生产效率、产能和制造品质,为客车快速发展奠定基础。
核心业务指标:宇通新能源工厂产线生产效率提升52%,资源利用率(能耗)降低36%,产品不良率下降41%,运营成本降低34%,产品研制周期缩短51%。
2)社会效益
随着宇通智能工厂制造体系的建立,将加快企业技术成果转化速度,全面提升企业竞争力,并通过资源共享、联合开发及沟通交流,拉动相关装备行业技术水平提升。举例如下:
高端管材锯切装备:形成设备开发、制造能力,并在自动化、柔性和材料利用率方面超越进口装备;
钣金加工装备:自动化成套技术方面,在目前的技术和市场几乎为零的现状上快速起步,逐步实现技术和国外同步,并形成一定规模;
机器人焊接系统:通过机器视觉(联合开发机器人弧焊视觉系统,达到国际水平)、焊接工艺专家库和柔性夹具系统的应用,促进机器人集成厂家在机器人高端应用领域的设计开发能力得到系统提升。
3)环境效益
一方面通过能源管理系统建设,实现了对能源介质使用参数的采集以及关键高能耗设备状态的实时监控,通过信息化平台实现了能耗状态的透明化、信息化管理,从而达到节能降耗的目的。
另一方面通过自动化、智能化设备的改造和新增投入,建立环境友好的智能化生产体系,从而减少噪音、粉尘、有害气体排放等污染,实现环境优化改善的目标。