数字化转型是个范围很大的话题,为了细化痛点并结合乳制品企业管理现状,避免讲空话,本次我们就把重点和范围聚焦在工厂生产管理的数字化转型上。
经验证,总体来说乳制品企业数字化转型可以实现现场数据自动采集,生产计划管理, 作业执行管理,生产标准管理,过程质量管理, 生产追溯管理,物料流转管理,设备运行管理,生产绩效管理,以及 ERP/WMS/LIMS 集成等功能,对下与自动化系统、控制 PLC,称量设备及过程仪表等进行互联,实现了 IT 与 OT 的融合,实现前处理、灌包装等环节的生产过程数据和设备运行数据的实时获取、监控分析和全程追溯,对上与原奶、ERP、WMS、LIMS、 包装追溯等系统集成协同,进行统一的数据交互。以此奠定智能制造平台基础,成为集团数字化、智能化目标实现的有力支柱。
系统蓝图
通过梳理各业务部门及管理层的需求, 结合乳制品企业现状并与系统功能的匹配,罗克韦尔自动化首先规划了集团及中央工厂的系统规划蓝图,以界定系统功能和范围,各司其职,减少功能重合和重复投资,实现生产全过 程追溯化 ;生产调度智能化 ;现场操作合规化 ;生产过程透明化 ;和生产数据集中化。
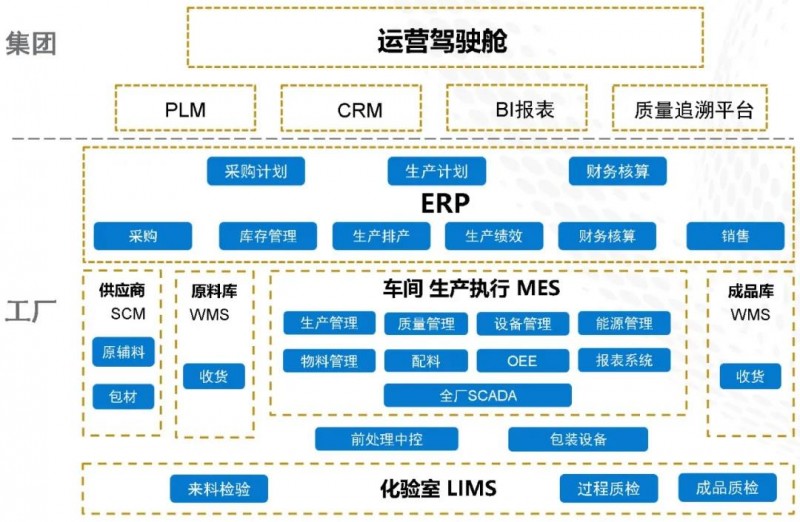
本次我们把重点放在以 MES 为核心的企业“数字化”转型需求和方案上。
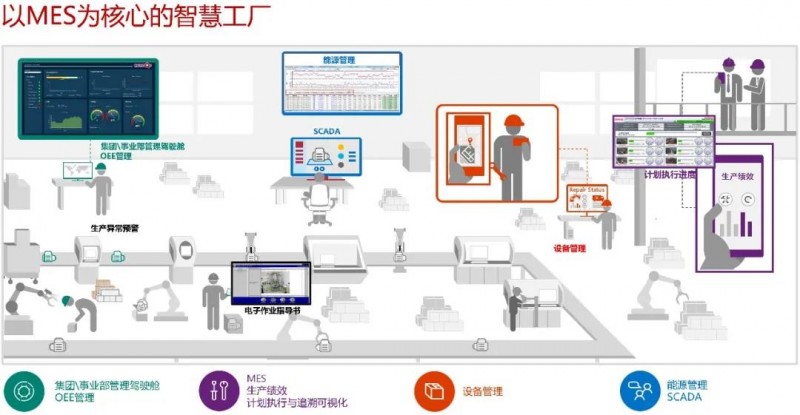
以下会从常见的生产,质量,设备,能源等四个乳制品企业核心部门需求与系统功能进行阐述,并从使用者角度讲述数字化转型对其工作方式和管理模式的影响 :
生产部门:
涉及到 SCADA,ERP 和MES系统的集成使用。从收奶开始一直到成品入库各个关键工艺段的管理,包括生产指令的下达, 物料的配料与核算,配方修改,标签管理,启动生产,生产指导,产出计算, 直到产生完整的生产报表等功能。
SCADA 能够通过 HMI 界面实时显示生产状态和关键生产参数,自动记录并整理成生产报表 ;
MES 系 统 通 过 接 受 从 ERP 发 送 的 工 单 和 BOM 信 息, 根 据 SCADA 获得的设备占用状态,自动拆解并下发到各设备操作工位,并依据电子 SOP 合规生产,实现系统操作步序的防错,生产完毕自动发送消耗信息给 ERP 报工 ;
在前处理投料和小料添加环 节,MES会依据配方进行工单校验, 称量复核校验,并与前处理中控集成(投料口电磁阀控制)系统自动放行, 实现投料三重防错 ;
三个系统的集成可以帮助生产部门提高沟通效率,生产信息透明化, 人员操作合规化,系统通过人、机、料、法、环等不同种类的数据再利用和数据分析,可以帮助客户更好的指 定黄金批次标准,和质量相关性分析,以稳定产量和质量,同时关联到班组和操作工个人的绩效考核指标评估,让数据发挥更大的作用,真正实现数字化助力生产。
质量部门 :
重点关注食品安全与合规,包括质量防错、追踪追溯和生产批记录等功能。主要涉及实验室信息管理系统 (LIMS), 全厂SCADA 系统和生产制造执行系统(MES)使用和对接 ;
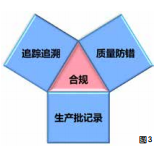
1、 其中 LIMS 负责原奶接收检验, 半成品检验,成品检验和过程抽检等实验室相关流程管理 ;
2、 SCADA 系统负责实时采集并 记录生产过程中所有质量相关的工艺参数,通过关键质量参数的阈值设定,实现实时的超限报警,实现产品生产过程中工艺符合性追溯的及时性,改善原有通过保温实验结果或市场投诉寻找工艺缺陷点的不足 ;
3、 MES 则负责质量配方,检测计划,问题升级流程,生产中质量相关点巡检(移动端)与质量放行,消息推送,作业指导,SPC 分析,质量和生产电子批记录等功能 ;
4、 MES 系统的另一个主要功能 就是完成订单生产过程中的追踪追溯,根据工单号,记录当批工艺配方, 操作步序,操作人员信息,当时的设备状态,质量过程参数,报警信息, 环境信息等数据完成正反追溯,实现 “人、机、料、法、环”的全面质量管理。
通过三大系统的集成,可以帮助质量部门实时了解生产状态及过程质量参数,异常预警及时处理,通过系统建立计划并跟踪检验结果,实时干预并回溯,以减少损失,提高质量稳定性和均一性。未来,利用已有的质量数据还可以与企业的投诉系统相关联,利用大数据分析,快速精准的定位问题产品批次及当批的生产质量信息,实现追踪溯源。
设备部门:
主要涉及 SCADA,OEE,设备管理系统使用。
SCADA 可以实时采集设备运行参数,故障信息并报警记录,通过故障信息采集,维修人员能够及时获取故障信息快速维修(实时短信提醒),通过故障维修时间计时,提高维修的效率,也为未来人员绩效考核提供依据 ;·OEE通过SCADA采集到的灌装设备数据实时计算整线或单机OEE,及手持终端实现实时OEE效率看板,操作人员能够实时掌握设备运转效率及过程问题,再结合TPM方法进行有效的改善,最终使设备发挥最大的生产效率 ;
设备管理系统涵盖了设备资产管理(设备台帐、设备改造),设备维护管理(设备预防性管理),设备点巡检管理(包括现场移动作业管理 系统),设备维修管理(设备知识库), 备品备件管理(与 ERP 对接),设备报表等功能模块。
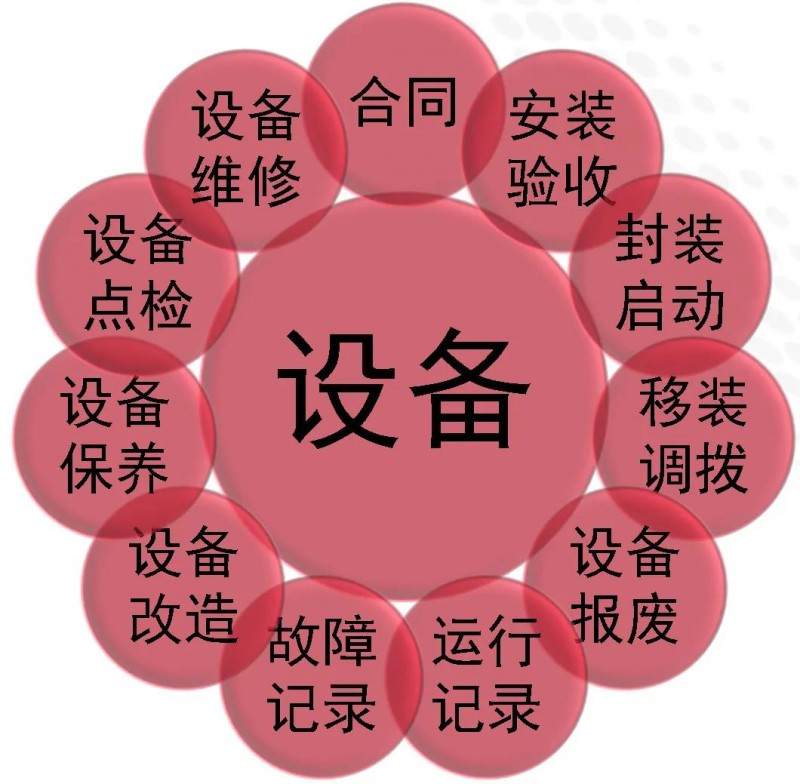
三个系统的集成可以为设备管理部门提供及时的设备动态和 OEE 分析结果,有重点的把脉瓶颈设备, 建立全生命周期的设备健康管理体系,从而减少停机时间和损失。
能源部门 :
涉及 SCADA 和能源管理系统的使用。
SCADA系统通过通讯从前处理成套设备读取已有能源数据,另外通过独立PLC自动采集质量流量计、源水表,纯水表,软水表,蒸汽表, 压缩空气表,电表等过程仪表数据, 实现计量牛奶、料液、水、蒸汽、压缩空气的过程使用数量,改变原来生产结束后倒推计算的方式。通过过程使用量能够准确发现具体的损失点, 从而结合精益生产的方法进行快速改善,提升成本管理精度 ;
能源管理平台通过从SCADA拿到的能源数据,可以实时查看当前值以及历史曲线,预警,自动生成能源报表(需量,耗量,趋势 )和预测曲线,同时通过与MES系统的交互,绑定前处理批次信息、产量信息, 码垛机批次信息、品项信息等,以便实现单品项,单批次,单班组,甚至生产单瓶产品所需能耗,并根据计算换算成二氧化碳排放量从而形成企业标准,也为未来KPI指标的考核提供依据 。
以上从工厂使用者角度阐述了数字化转型给他们带来的改变, 通常来说数字化转型会涉及到企业所有的部门,从生产部门到财务部门, 从一线员工到高层管理者都会用到这一系统,所以系统的成熟度就尤为重要。
方案成熟性
作为罗克韦尔自动化实现上述 功能的核心解决方案 CPGSuite® 套件,获得了“2020 中国自动化年会-最具价值解决方案“,其基础平台FactoryTalk Production Center( 简称 FTPC) 从软件研发之初到如今已经发展了 15 个年头,10 个版本的更新, 全球有上百家工厂,上千个用户在使用此平台,在食品饮料行业例如雀巢, 玛氏,卡夫,芝华士,康尼格拉,恒天然,雅培,阿拉等全球客户,和国内乳制品客户,例如贝因美,伊利, 味全等,尤其伊利项目申请的《乳品生产智能工厂试点示范》获得了国家智能制造 2015 年智能制造试点示范项目及由 e-works 评选的 “2020年中国智能制造标杆工厂”的称号。
数字化转型收益
以某品牌为例,罗克韦尔自动化从 2007 年开始与出口排名全球第一的某集团(新西兰最大的乳制品集团)合作部署 MES 试点工厂, 到如今已经部署了 25 家子工厂,总体产量提高大约8%,实现生产全过程的追溯,并满足出口法规的要求,另外MES的部署使得恒天然在生产,质量,设备管理,KPI 指标计算、考核,工厂建设等的企业级标准化方面有了很大提升,也为其实现数字化转型之路迈了一大步。
总结
数字化转型之路并不易走,其中不乏实施失败的案例,罗克韦尔自动化也总结出自己的建议供大家参考 :
认清自我 :理清现状,制定目标,规划优先 ;
分布实施 :试点为先,先易后难,标准先行 ;
坚定决心 :领导带队,负责到底,部门协同 ;
跨行借鉴 :跨行业借鉴经验和技术。