利德华福从2017年开始全面部署“智能制造“战略。在制造流程中,从客户订单接收、来料检验、生产制造、客户验收及产品运输等环节,打造了端到端的全供应链数字化系统。
在2020年世界级先进管理体系Gartner全球供应链评比中施耐德电气排名第4位(工业变频器领域第一名)。
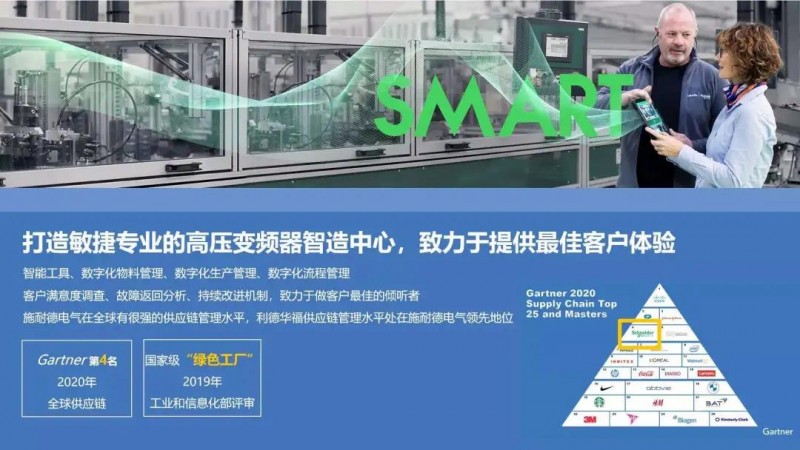
搬起小板凳,故事开始啦~
我,
是利德华福Harsvert系列高压变频器
家族中的一员,
一位体积庞大的能效专家。
大家会不会好奇“我”是怎么生产出来的呢?
一路上都经历了什么?
那么就让我带领大家来开启
高压变频器制造的“链动之旅”吧~
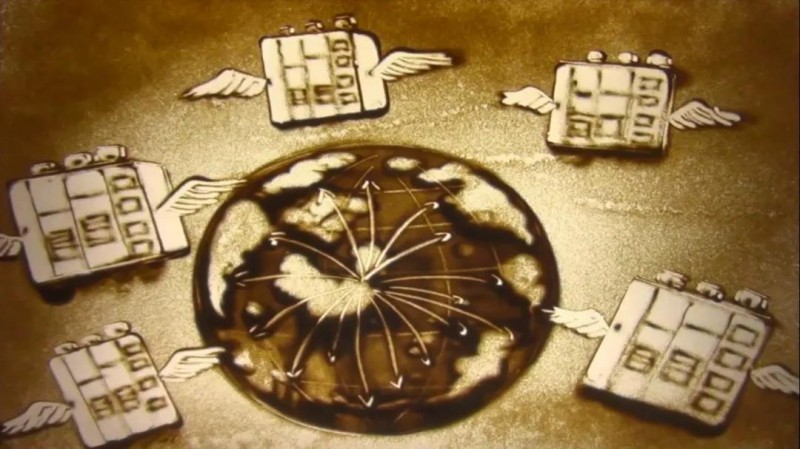
今年3月底,那时新冠疫情正在疯狂的在人们的生活中传播,利德华福工厂供应链计划部门接到西藏某水泥厂紧急发货的需求:客户要求4月14日发货,这个需求日期大大短于标准交货期。与此同时,该项目是将投运于3500米高海拔的特殊设备,货期紧急且任务艰巨,让我们来看一下供应链部门的同事是如何应对的吧~
供应链计划部门将客户的发货需求时间录入到电子排单系统(E- scheduling),根据发货时间自动反馈出开始生产加工的时间及加工的位置信息。
同时E-scheduling系统的缺件管理模块(ATP check)自动分析出生产加工所需要的原材料库存是否能满足生产加工时间。当库存不能满足生产加工需求时,系统会发出提醒给采办的小哥哥、小姐姐们,他们会追踪供应商并确认加急到货时间。
这个项目还有一些特殊定制的物料,采办的小哥哥、小姐姐们积极与供应商沟通,安排供应商优先加急生产,缩短供应商加工周期,将原材料按时送到工厂。
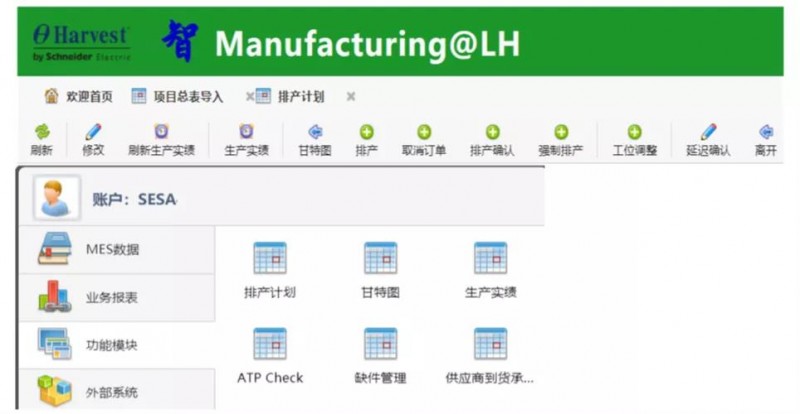
原材料到达工厂入厂检验合格后,会收录到仓库指定库位进行存储,仓库管理员通过物料备料电子系统(E-Kitting)将生产加工所需的原材料清单打印出来进行拣货,并送到生产线上。
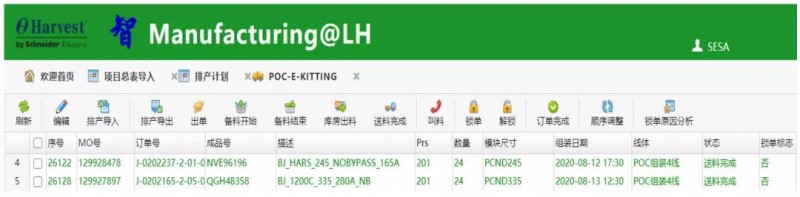
生产线的小哥哥、姐姐们对组装加工的关键零部件进行扫描,将关键零部件的批次信息,出生地,记录到物料追溯系统(E-Traceability)中。
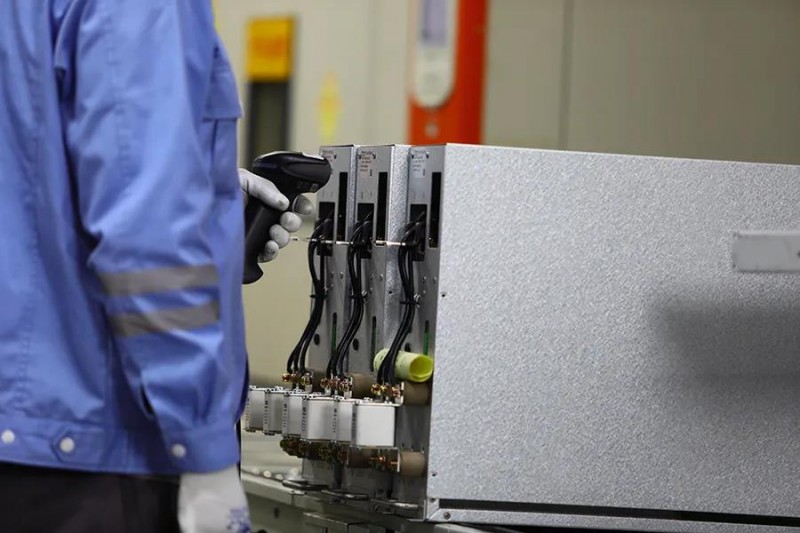
关键零部件扫描到物料追溯系统(E-Traceability)中
过了几天,我的骨架“机柜”、“变压器”、我的肋骨和肌肉“功率模块”、我的大脑“主控箱”、我的漂亮的脸庞“HMI”(人机界面)都已经装入到我的身体中。生产线的小哥哥们开始对我进行测试,检测我的身体是否按照我的大脑指令在运行。
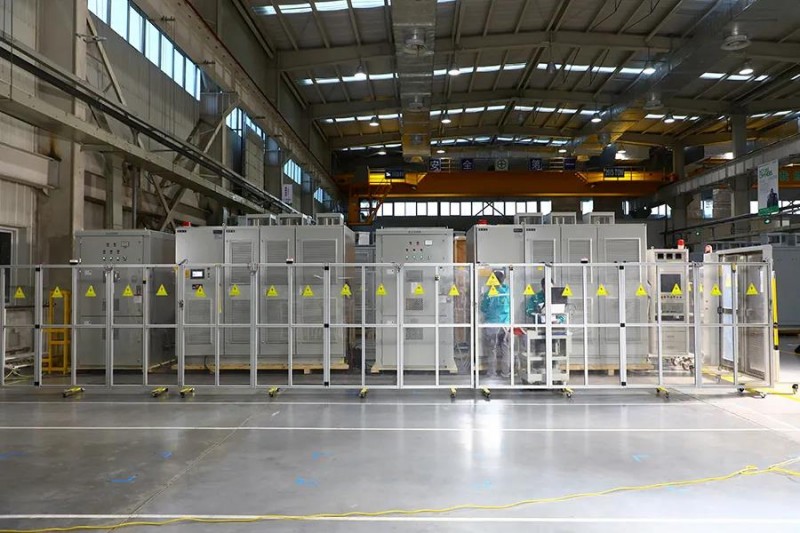
高压变频器整机测试
“我是怎么了,貌似身体不能按照大脑的指令工作了” !正当我焦虑地不知所措时,供应链计划部门的小姐姐找来研发、设计、质量的工程师“医生”们来到现场帮我诊断“病情”,通过对我的关键零部件扫描记录信息进行分析诊断,很快找到了“病因”,并开出“药方”,生产线的小哥哥们按照工程师“医生”的“药方”执行,很快我的身体运行正常。
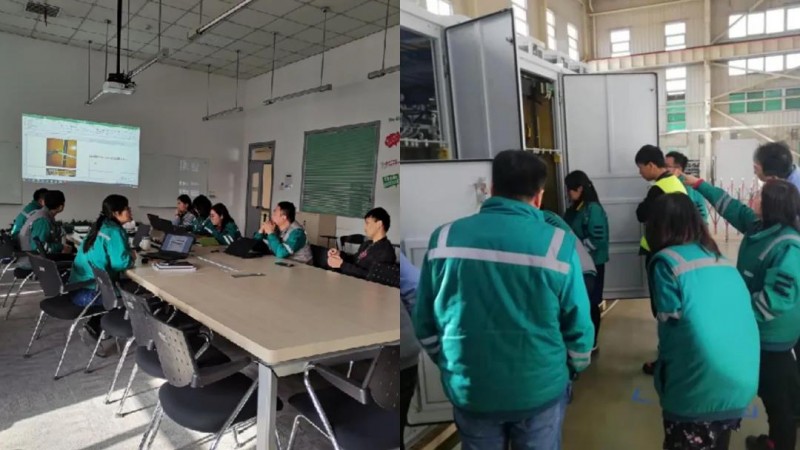
各职能部门在讨论高海拔特殊设备的问题解决方案
4月14日,也就是客户期望的交货期当天,我高兴地穿上了厚厚的木质外衣,踏着轻盈的步伐,等待被送往客户现场,负责运输的小哥哥在我的外衣上安装了漂亮的胸针—“GPS定位装置”,运输过程中实时监控我乘载的车辆行进状态,如发现异常可以立即反馈给项目负责人。几天后,我被安安全全地交到客户手中。

GPS定位装置
作为一台高压变频器
“我”的链动之旅故事讲完了
您是否意犹未尽呢?
诚挚的欢迎您莅临“华丽丝”
北京利德华福电气工厂
身临其境的来一场“链动之旅”!