我国工业正在经历数字智能化的崛起,我们曾经头顶光环 (IPv6) 站在世界之巅,网络空间霸权也使我们脚踏尘沙,“雪人计划”让我们终于迎来机会,工业重构必然是燎原烈火。随着新赛道的开启,以及信息化、数字化、融合化、智能化的发展,工业智能化未来可期。虽然供给侧结构性改革能解决快速实施的问题,但是网络安全发展越来越复杂化,IoT融合安全道阻且长,网络安全必须向更高级进化。虚拟化、数字孪生是提升实力的必由之路,各个行业需借助数字孪生技术推进行业的创新发展。
工业网络的核心是控制系统,工业网络安全建设的最终目的也是保护工业安全,但当我们不了解其机理、状态和问题驻留情况时,就好像在自己家里放了一个放射物质,我们却全然不知。虽然我国对DCS系统的研究发展与国外几乎没有技术代差,但是仍存在一定差距。在硬件方面,核心芯片受制于人,工业软件发展缓慢,工业控制技术影响先进工艺流程的开发和发展,因此很难进入某些高端行业领域或特殊工艺的业务场景。由于我国在早期大量引入国外DCS系统,也造成国内市场的自主品牌在很长一段时间举步维艰,一旦市场或国际形势发生变化,很容易造成断供、断货,工业行业亟待开启新的征程。
顺大势,谋未来。数字化新时代的大门已经敞开,新的机遇与挑战纷至沓来。如何顺应工业互联大趋势、运筹帷幄,最终抢占时代先机?作为国民经济的重要信息安全支撑产业,网络安全(尤其是工控安全行业) 也在积极寻求突破,拓“智”能发展,“维”新路径,助力行业产业链以及宏观经济的可持续发展。本文讲述依据数字孪生技术开发DCS数字孪生体,构建DCS的众测验证平台,在DCS物理世界中,通过数字孪生技术复制n份数字孪生体,为DCS系统提供设计验证、故障模拟数据联动、智能预警、智能控制等功能应用控制和操作环境。
数字孪生背景
通俗来讲,数字孪生(Digital Twin,DT)是指针对物理世界中的物体,通过数字化的手段构建一个在数字世界中一模一样的实体,借此实现对物理实体的了解、分析和优化。从技术角度而言,数字孪生集成了建模与仿真、虚拟现实、物联网、云边协同以及人工智能等技术,通过实测、仿真和数据分析来实时感知、诊断、预测物理实体对象的状态,通过指令来调控物理实体对象的行为,通过相关数字模型间的相互学习来进化自身,合理有效地调度资源或对相关设备进行维护。
2002年10月在美国制造工程协会管理论坛上,当时的产品生命周期管理(Product Lifecycle Management,PLM)咨询顾问Michael Grieves 博士提出了数字孪生最早的概念模型。但是,当时“数字孪生”一词还未被正式提出,Grieves博士将这一设想称之为“PLM 的概念设想(Conceptual Ideal for PLM)”。
2009年,美国空军实验室提出“机身数字孪生(Airframe Digital Twin)”概念,将数字孪生概念应用于航空航天制造领域。2010年,美国国家航空航天局在《建模、仿真、信息技术和处理》和《材料、结构、机械系统和制造》两份技术路线图中直接使用了“数字孪生”这一名称,并将其定义为“集成了多物理量、多尺度、多概率的系统或飞行器仿真过程”。2011年,Grieves博士在其所著的《智能制造之虚拟完美模型:驱动创新与精益产品》中正式定义了数字孪生概念,并一直沿用至今。
2012年美国空军研究室将数字孪生应用到战斗机的维护中,而这与航空航天行业最早建设基于模型的系统工程(MBSE)息息相关,能够支撑多类模型敏捷流转和无缝集成。近些年,数字孪生应用已从航空航天领域向工业各领域全面拓展,西门子、GE等工业巨头纷纷打造数字孪生解决方案,赋能制造业数字化转型。数字孪生蓬勃发展的背后与新一代信息技术的兴起、工业互联网在多个行业的普及应用有着莫大联系。
各国数字孪生发展情况
(一) 美国
美国从战略规划、应用实践、产业创新等方面全方位布局数字孪生发展。
一是“政产研”合力推动数字孪生上升为国家战略。二是依托航空航天基础优势,探索形成了成熟的应用路径。三是供给侧企业加快技术创新,利用新一代信息技术优化数字孪生应用效果。如在“IoT+仿真”方面,ANSYS和PTC公司合作构建水泵的数字孪生体,实现实时数据驱动下的仿真诊断,相较于传统离线仿真,大大提升了诊断的及时性和准确性。在“AI+仿真”方面,MathWorks将数据分析工具MATLAB和仿真产品Simulink打通,将MATLAB人工智能训练数据集输入Simulink 中进行仿真及验证分析,极大地优化了仿真结果。
因此,美国数字孪生的综合优势体现在在三个方面:一是构建了基于模型的系统工程方法论,通过统一语义和语法标准、给定系统集成路径,为数字孪生应用提供理论指导。二是拥有强大的仿真产业,ANSYS、MathWorks、Altair等企业为数字孪生应用提供基础建模工具。三是拥有丰富的应用数据和模型,空客公司、洛克希德马丁公司、特斯拉公司等企业在产品研制过程中积累了大量机理模型,持续优化数字孪生精度。
(二) 德国
德国立足标准体系基础,加快打造数字孪生竞争优势。
德国立足标准制定基础优势,面向数字孪生打造了数据互联、信息互通、模型互操作的标准体系(即管理壳理论),实现各类数字化资产(数据、信息、模型)之间的无缝集成融合,提升物理实体在虚拟空间映射的精准度。在数据互联和信息互通方面,德国在OPC UA协议中内嵌信息模型,实现通信数据格式一致性。在模型互操作方面,德国依托戴姆勒的Modolica标准开展多学科联合仿真,目前已经是全球仿真模型互操作的最主流标准。同时,2020年9月,德国VDMA、ZVEI、Bitkom联合20家欧洲龙头企业(ABB、西门子、施耐德、SAP等)成立了工业数字孪生协会,其目标是通过统一各个企业数字化工具标准,提升数字孪生体的并行开发效率。
此外,相较于美国更多开展“装备级”数字孪生,德国具有单点优势,西门子是全球极少数能够提供“工厂级”数字孪生的工业服务商。近10年来,工业自动化巨头西门子花费100多亿美元收购了几乎全类别的工业软件,涵盖了产品生命周期管理(Teamcenter)、计算机辅助设计(NX)、电子设计自动化(Mentor)、事件仿真(Simcenter)、制造运营管理系统(Opcenter)等,并持续将各类工业软件集成到MindSphere工业互联网平台。在此基础上,西门子能够基于平台构建全工厂数字孪生,不仅能够实现虚实映射,还能基于工业自动化优势完成闭环控制。
(三) 中国
中国数字孪生市场活跃,多主体参与市场,但创新能力有待提升。
中国各类主体积极参与数字孪生实践,在理论研究、政策制定、产业实践等方面开展探索,但整体上应用深度和广度还需进一步拓展,仍待挖掘更多的工业应用场景。
在理论研究方面,中国关于数字孪生思想的研究由来已久,1978年钱学森提出系统工程理论,由此开创国内学术界研究系统工程的先河。2004年,继美国提出数字孪生概念,中国科学院自动化研究所的王飞跃研究员聚焦解决复杂系统方法论,首次提出平行系统的概念,将系统工程与新一代信息技术结合。
在政策制定方面,2021年我国各部委和地方政府开始纷纷出台数字孪生相关政策文件。国家发展和改革委员会的“上云用数赋智”、中国科协的“未来十大先进技术”、工业和信息化部的“智能船舶标准”均将数字孪生列为未来发展的关键技术,上海和海南在其城市规划中也提出要打造数字孪生城市。
在产业实践方面,我国多类主体均开展数字孪生探索,如恒力石化、中广核技等企业积极构建三维数字化工厂,湃睿科技、摩尔软件等企业利用AR、VR提升数字孪生的人机交互效果,工业自动化企业华龙迅达构建虚实联动的烟草设备数字孪生。尽管我国多类主体探索数字孪生的热情高涨,但大多数产业实践停留在简单的可视化和数据分析,与国外基于复杂机理建模的分析应用还存在一定差距。
与数字孪生相关的政策措施
2020年,“新型基础设施建设”首次写入2020年政府工作报告,“数字孪生”被不少人大代表和政协委员所提及。2020年4月,国家发展和改革委员会印发《关于推进“上云用数赋智”行动培育新经济发展实施方案》,方案中提出要解决企业数字化转型所面临的数字基础设施、通用软件和应用场景等难题,利用数字孪生等数字化转型共性技术、关键技术的研发应用,引导各方参与提出数字孪生的解决方案。数字孪生技术的受关注程度和云计算、人工智能、5G一样,已经上升到国家高度。
DCS数字孪生体的需求分析
集散控制系统DCS是一个集结构、电气、控制、热力、信息等多学科于一体的分布式控制系统,该系统用来实现不同工况下工艺的生产、过程控制、专设保护设施驱动,系统状态控制指令等功能。在工艺设备的运行过程中,来自现场的传感器会向DCS传输大量现场物理量信息,通过逻辑运算得出相应逻辑指令,同时机柜自身也会产生非常多的状态信息和测试信息,这些信息长期没有得到很好的关联。在DCS产品数字化过程中,传统的设计理念和方法容易产生“信息孤岛”和“信息重复”的问题,DCS产生的动态信息流无法被实时调度以及协同处理。
通过借鉴数字孪生技术的优势,重点研究集散控制系统DCS在不同行业中对数字孪生技术的应用及开发,利用虚拟的DCS孪生环境,可以完成DCS设计验证、故障模拟、数据联动、智能预警、智能控制等功能应用控制和操作。基于实体DCS系统构建DCS数字孪生体的过程可分为如下三步。
1)搭建物理实体DCS系统环境,DCS系统(包括控制器、采集模块、通信模块和相关控制应用软件等)可以选用不同的品牌。
2)构建DCS孪生体,可以仿真建模实物DCS,构建DCS系统数字孪生体,DCS孪生体需具备以下功能:
?DCS数字孪生体操作和管理模块;
?DCS数字孪生体仿真和服务模块;
?DCS数字孪生体资源接入和交互模块;
?DCS数字孪生体资源组件。
3)建立DCS数字孪生体测试床,借助应用展示接口为用户提供实体交互能力、感知能力,通过DCS数字孪生体构建出的测试床将通过数字孪生技术复制出一个数字孪生体。
DCS数字孪生体的设计方案
(一) DCS数字孪生体总体架构设计
DCS数字孪生系统通过与物理世界不间断地交互和反馈闭环信息、融合数据,能够模拟对象在物理世界中的行为,检测物理世界的变化,反映物理世界的运行状况、评估物理世界的状态,诊断发生的问题、预测未来趋势,甚至优化和改变物理世界。在数字孪生体中引入安全监测、测试验证等工具,可以支持DCS安全检测功能,通过数字孪生系统完成设计验证、故障模拟、数据联动、智能预警、智能控制等功能应用控制和操作。
结合项目DCS数字孪生体的需求基础架构和能力特点,DCS数字孪生体系架构,可以参考面向制造业的数字孪生体系架构标准ISO/DIS 23247,该标准虽然是面向制造业的数字孪生体系架构,但考虑到ISO标准的专业性和权威性,相关架构能够从很大程度上反映DCS数字孪生体的关键要素和核心内涵。DCS数字孪生体的框架如图1所示。
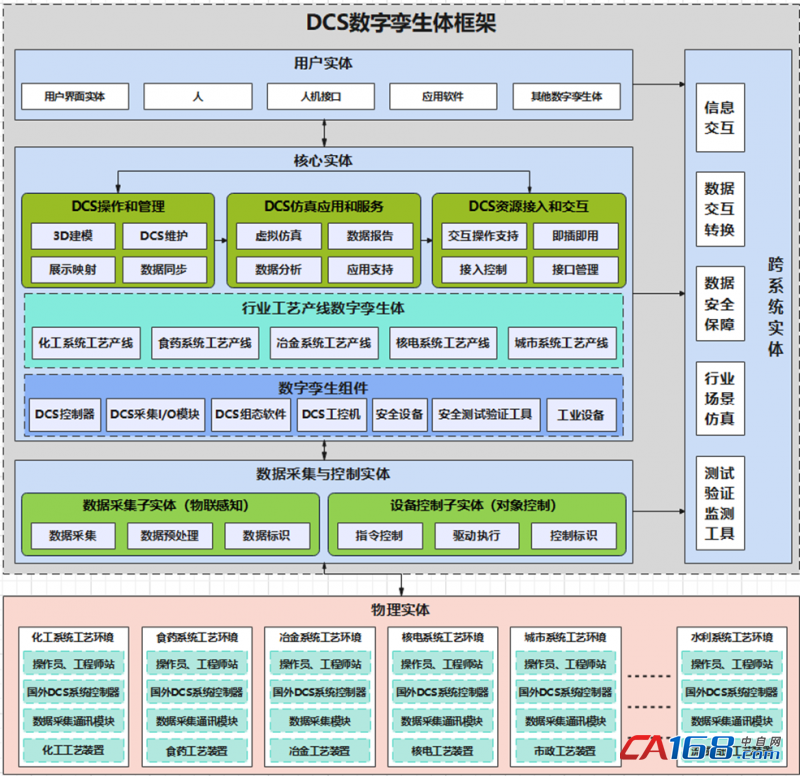
图1 DCS数字孪生体的框架
DCS数字孪生系统包含以下三层。
一是数据采集与控制实体,主要包括数据采集子实体(物联感知)与设备控制子实体(对象控制)。数据采集子实体通过监测和传感设备面向物理对象收集信息,实现物理对象与数字孪生体之间的信息同步,具备数据采集、数据预处理以及数据标识等核心功能。设备控制子实体控制和驱动物理对象,具备指令控制、驱动执行、控制标识等核心功能。
二是核心实体,核心实体负责将物理对象映射为数字孪生体,从而进行维护,包括DCS操作和管理、DCS仿真应用和服务、DCS资源接入和交互三个子实体。DCS操作和管理子实体支持对物理对象的数字化建模、描述、展现、同步,以及对整个核心实体的操作和管理、DCS仿真应用和服务子实体支持系统仿真、数据分析和报告等功能,而DCS资源接入和交互子实体向上层的用户实体层提供对核心实体功能的访问。作为核心实体的重要组成部分,数字孪生组件是构建工控业务场景的重要基础,组件可以构成组建资源池,借助DCS操作和管理模块,用户可以构建行业工艺业务基础环境。
三是用户实体,面向利用数字孪生体实现制造应用的用户,包括人员、设备、应用(MES/SCADA)等,实现高效的人机交互。
除上述三层外,DCS数字孪生体系的架构中还包括跨系统的各类实体,用于实现不同层之间的数据转换,提供数据准确性、完整性和安全性保障。
物理实体可以包含多种不同国外常见品牌的DCS系统物理实体,用于DCS系统及行业系统工艺映射适配。DCS数字孪生体构建的测试床将DCS实物测试床(物理实体)通过数字孪生技术复制出一个数字孪生体。
数据采集与控制实体、核心实体(数字孪生)以及用户实体之间的数据流和信息流传递,需要信息交换、数据保证、安全保障等跨域功能实体的支持。通过工业协议,可以实现数字孪生之间交换信息。安全保障负责数字孪生系统安保相关的认证、授权、保密和完整性。数据保证与安全保障确保数字孪生系统数据的准确性和完整性。
(二) DCS数字孪生体技术架构设计
DCS数字孪生体技术架构包含基础层(IaaS)、数据层(PaaS)、应用层(SaaS)。其中数据层包括感知层、传输层和平台层,DCS数字孪生体技术架构的设计如图2所示。
接下来将对DCS数字孪生体技术架构中的基础层、感知层、传输层、平台层和应用层进行介绍。
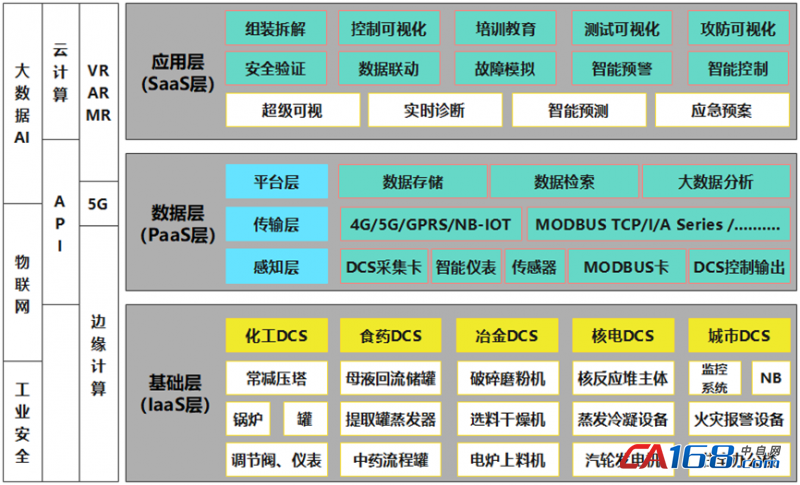
图2 DCS数字孪生体技术架构的设计
基础层:以化工、食药、冶金、核电、城市等底层基础物理设施为依托,实现真实空间与虚拟空间之间的双向数据互通、指令控制、虚实联动。
感知层:以高精度、高灵敏的PLC、DCS、采集板卡、智能仪表、物联网传输设备、ZigBee、控制输出板卡等传感器系统是实现DCS数字孪生系统的基础和万物互联感知的入口,通过采用这些系统实现虚拟工业行业场景中对物理场景的全息复制和动态调整。
传输层:异构通信技术,数字孪生系统面临多系统、大连接、海量数据的双向传输需求,要利用宽带(4G、5G、GPRS、NB-IoT)、窄带(RS-485、M-Bus、HPLC、Lora、RF、Ethernet)等新型异构网络技术实现高速率、高容量和低时延接入,确保物理电网海量传感器的接入要求和虚拟电网精准控制指令的传达要求。
平台层:数字孪生模型构建与自我优化依赖全域全量的电网数据,借助于数据中台的数据存储、检索和大数据分析能力,实现超大规模全量多源数据的安全存储、高效读取,为数字孪生平台优化决策提供精细的数据要素。
应用层:基于数字孪生技术对电力系统主要设备、厂站与环境精细三维全景仿真,实现与采集数据的实时交互,在安全验证、数据联动、故障模拟和诊断、智能监测与预警、智能控制输出等各个应用场景中,动态融合展示设备与关键传感数据。应用从超级可视化到实时诊断、智能预测、应急预案等多场景中。
(三) DCS数字孪生体功能设计
根据项目需求,构建数字孪生体是本项目的核心关键件,DCS数字孪生体可以提供仿真研究服务,DCS数字孪生体仿真服务将根据DCS实物模拟一个仿真模型,可以复制DCS资产的运行情况,也可以通过基本物理原理分析来预测DCS的运行情况。
采用Emulab软件进行仿真,根据用户提交的NS配置脚本,为用户构建一个具备真实网络组件的模拟实验网络,用户可以直接对实验网络中的每个节点安装操作系统、系统软件和应用软件,从而进行各种网络模拟实验。基于Emulab的模拟技术综合了软件与实物仿真技术,可以实现各层网络协议、多种网络服务以及应用程序的模拟,仿真度高。与此类似的网络模拟实验床还有DETERLab、PlanetLab等。之所以要采用Emulab、DETERLab这类模拟实验床来建立DCS系统的网络拓扑,是因为要研究DCS系统通信网络的安全性和适应性,就必须掌握与所有计算机网络故障有关的功能、行为和状态,其中很多是未知的,传统的NS-2、OMNeT++等网络仿真软件难以满足这样的要求。而以Emulab、DETERLab等为代表的一些网络实验模拟平台,以其特有的软件系统和基于真实网络设备的特点,已逐渐成为目前的主要技术手段。
仿真模型结合数字孪生体建模管理,利用物联感知技术、采集技术对DCS的模型进行3D建模,通过CAD等建模软件,3D孪生体可以根据实物的模型尺寸进行虚拟化的3D模型还原和绘制,为数据的运行和状态显示提供虚拟的孪生操作实体集合。然后基于DCS的工控通信协议,建立仿真协议通信接口和运行模型,完成通信网络的建立。
DCS数字孪生体还为应用模块(孪生共智)提供交互接口,使用人机接口或API接口操作,包括人、人机接口、应用软件和其他相关数字孪生体。DCS数字孪生体也为DCS安全检测功能提供数字孪生系统支持设计验证、故障模拟、数据联动、智能预警、智能控制等功能应用控制和操作。DCS数字孪生体应用模块可以控制DCS数字孪生体,并使用与实际物理资产相同的控制软件和人机界面去开发其人机界面。接下来,工程师可以通过使用这个与物理设备相同的控制接口,虚拟地测试数字孪生体在不同场景下的表现或操作条件,以查看物理设备的性能。
此外, DCS数字孪生体会仿真建模实物的DCS,同时实现DCS的工控协议仿真和通信协议建模,并且实现黑盒还原的DCS运行机制算法库模型。DCS数字孪生体将DCS实物控制器和典型行业工艺流程分别建模,建立DCS数字孪生体测试床,并根据相互之间的关系进行更高级别的合成,用于构建工控仿真场景中的控制单元,同时控制器还将成为测试系统中的测试靶标。DCS数字孪生体还将实现与行业实物工艺流程和行业仿真工艺流程片段数字孪生体组合使用,实现虚实结合的增强模拟测试床灵活组网和构建,借助测试管理平台构建行业测试床,用户可以通过Web随时随地接入测试。
DCS数据孪生系统的功能应用架构如图3所示。
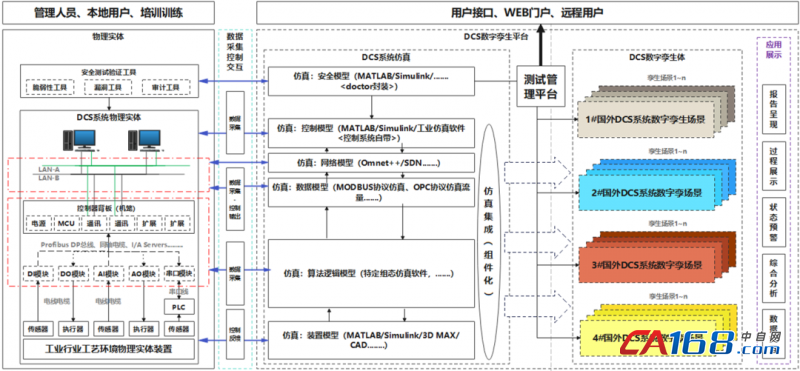
图3 DCS数据孪生系统的功能应用架构
DCS数字孪生系统具备以下6个功能。
1.真实可视化
通过对控制站硬件的拆解、安装和维护操作,真实还原了控制系统硬件集成的全过程。
2.设计验证
通过正确地选择、组合、安装和设置DCS数字孪生系统,进一步保证了真实DCS系统的安全稳定运行。
3.数据联动
通过二维和三维仿真数据的实时交互,全方位、立体式地展示控制系统的生产运行过程,辅助工程师快速掌握控制系统的结构,直观解读控制系统传递的数据。
4.故障模拟和状态监测
对真实环境中,再现硬件与软件在正常状态和异常状态下的联动过程,完整地实现了DCS系统从软件到硬件的交互过程。
DCS数字孪生系统能够实现行业业务场景的复杂控制,尤其是在冶金高炉、化工流程控制、高端智能装备制造业务环境中。在控制系统运行过程中,将实时采集的传感器数据传递到其数字孪生模型中进行仿真分析,诊断DCS控制系统的健康状态,从而进行故障预测。如果控制系统运行的工况发生改变,优化工艺控制策略,对于拟采取的调整措施,可以先在仿真平台上对其数字孪生模型进行虚拟验证,如果没有问题,再对实际产品的运行参数进行调整。在复杂装备的运维方面,甚至可以通过AR技术,基于DCS系统的数字孪生模型生成工艺组态、逻辑组态、服务器组态、下载与上传操作、在线仿真等操作的三维动画。在实物环境下,可以通过各种穿戴设备或移动终端进行示范教学。
5.预警功能
DCS数字孪生系统可真实展现DCS系统的自我诊断保护、预警功能,在与仿真系统实时交互的共享数据流基础上,可对控制站进行系统级、模块级、通道级的故障模拟预警,辅助生产人员制定反事故措施能力,为企业安全生产保驾护航。
6.安全测试
通过项目提供的安全防护、检测、测试等工具,利用仿真技术进行孪生复制,结合DCS数字孪生体、行业工艺产线孪生体,可以实现DCS系统在安全合规防护、安全漏洞测试、脆弱性验证等方面的测试研究,加强生产人员对DCS系统的安全认知,对控制机理、安全后门有更深的认识。
结语
基于用户的数字孪生应用需求,三维DCS数字孪生系统具备大数据分析、在线寻优、自学习、自诊断等功能,支持预测控制、自整定、鲁棒控制等先进控制算法,助力企业实现智能化控制转型。
DCS数字孪生系统基于完整的设备信息模型,通过三维可视化技术真实再现了DCS系统,准确描述了DCS设备的真实状况,从而实现了以设备模型对象为基础的性能分析,支持与真实系统的数据实时交互。DCS数字孪生系统是现代智能工厂的核心组成单元,系统可与真实DCS及激励式仿真系统无缝对接,具备自我感知、在线操作、数据联动预警、故障模拟演练等功能,能够快速发现和解决生产过程中出现的控制系统故障,保障企业的安全生产运行,真正帮助企业降低生产运维成本、提升生产效率。
DCS数字孪生系统的自我感知能力使得该系统具备真实可视化和设计验证功能,对于DCS主控制站内的所有硬件设备,可进行控制站硬件拆解、安装和维护操作,真实还原了控制系统集成的全过程。通过正确地选择、组合、安装和设置DCS数字孪生系统,进一步保证了真实DCS系统的安全稳定运行。
DCS数字孪生系统的数据联动,可实现二维和三维数据的自动交互,全方位、立体式地展示生产运行过程,辅助工程师快速掌握控制系统结构、直观解读真实控制系统传递的数据信号,支持系统冗余,在与现场DCS及激励式仿真系统实时交互的共享数据流基础上,真正做到了与DCS系统融为一体,可真实再现DCS系统的自我诊断保护、预警功能,可对控制站进行系统级、模块级、通道级的故障模拟预警,辅助生产人员制定反事故措施,为企业安全生产保驾护航。