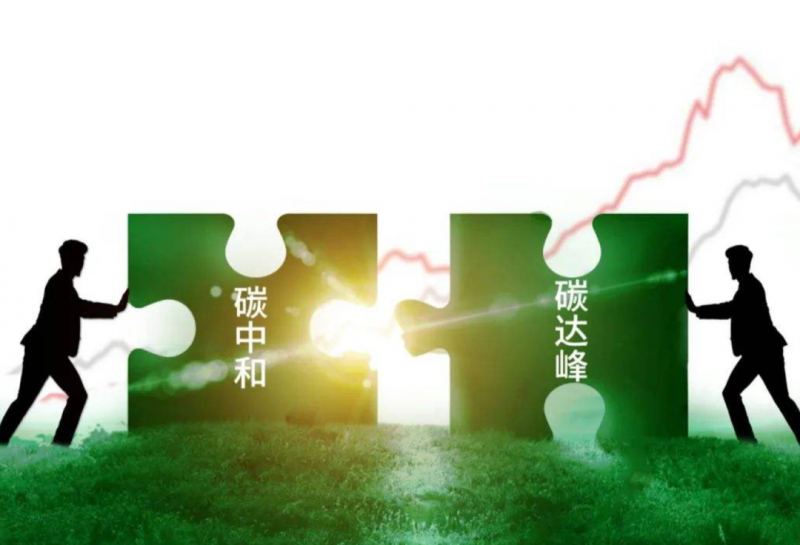
电池企业“降碳”需要关键设备技术创新
电池生产占汽车生命周期碳排放主要部分。根据欧洲运输与环境联合会(T&E)的报告显示,电池生产的碳排放范围在61-106kg CO2/kWh,约占据电动汽车全生命周期碳排放的60%以上。电池生产设备是主要能耗部分,解决关键设备的碳排放问题是电池企业“双碳”之路的重中之重。
电池前段生产环节的涂布工序,约占产线能耗30-40%左右,是电池生产能耗的“大老虎”。涂布机的绝大部分能耗产生于极片的烘烤过程,烘烤部分的能耗控制对于整个电池生产能耗管理意义重大。为了追求产能、高速,生产动力电池的涂布设备多采用折返式双层烘箱设计。折返式涂布的工作流程:箔材放卷后,先进行A面涂布,然后极片进入下层烘箱烘烤,再进行B面涂布,极片再爬坡进入上层烘箱烘烤,最后收卷。而SDC涂布,箔材放卷后,A面B面同时涂布,极片进入烘箱烘烤,最后收卷。相对于折返式涂布机,SDC涂布机直接节省出一层烘箱。同样产能情况下,SDC综合能耗节约30%以上,大大降低了能耗。
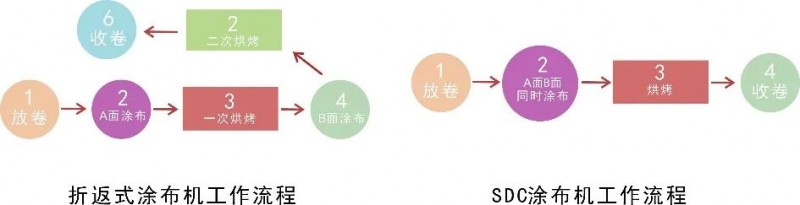
电池企业全面降低生产设备的能耗,并解决关键设备的能耗问题,能让节能减排事半功倍,锂电设备企业的技术创新实力在设备端发挥重要作用。
借助SDC提质降本增效,电池企业轻松化身“碳”路者
提质降本增效是整个锂电产业链一条不可避免的必经之路。电池企业通过提升产品质量、降低经营运行成本和增加整体效益 ,可加速“降碳”目标管控。
提升电池性能可为电池产品质量及竞争力“增砖添瓦”。SDC涂布通过料源来自同一料罐,并同时供给,A面B面干燥一致,“防抖动+真流道仿真”专利型模头设计,让面密度更加均匀;SDC烘箱的前1/3箱体采用开孔专利加热,高容设计也可高倍率放电;极片不卷边,极片表面无裂纹,涂层附着更好;可实现500PPM以下极片干燥度。以上,SDC为电池性能提供充分的技术保障。
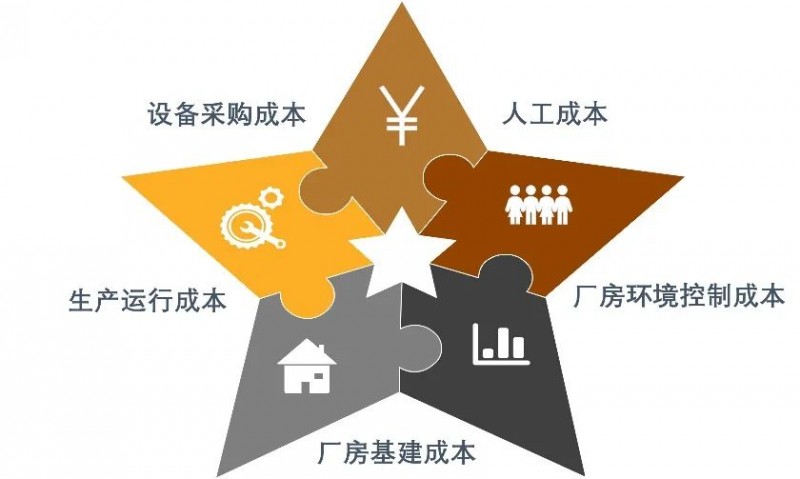
SDC为生产企业的成本管控提供省心省力解决方案。企业的电池项目规划上,可直接通过SDC降低采购成本、生产运行成本、厂房基建成本、环境控制成本以及人工成本。经过测算,厂房设备运行生命周期内,综合成本下降比例高达30%,实属难得。
优势技术的创新设备是企业增加效益的利器,是加速产业升级的“催化剂”,是“双碳”时代趋势的工业“驱体”。
全面SDC标准化,形成产业“降碳”规模效益
3月18日,工业和信息化部装备工业一司发布了2022年汽车标准化工作要点。其中就涉及要强化标准全生命周期管理,加快新能源汽车领域标准研制,助力产业转型升级,强化能源消耗量领域和碳排放领域的绿色技术标准引领,支撑“双碳”目标实现。
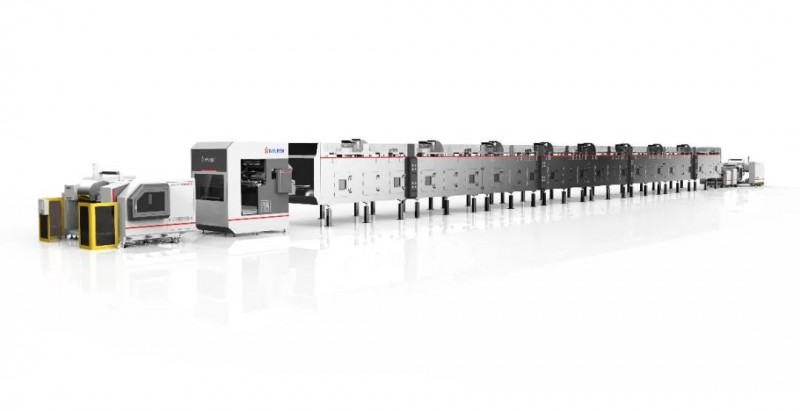
SDC(单向双面同时涂布机)
产业转型升级需要全产业链上下游共同标准化体系推动。信宇人SDC涂布机针对不同产业市场,推出动力、3C与储能等标准机型和配置,以产品标准化、量产化、规模化的方式推进产业标准升级。以SDC涂布标准化为代表,更大力度在设备端快速引领推进绿色技术标准,是实现产业规模效益、产业“双碳”目标的有力保障。
SDC涂布机行业应用现状
SDC涂布机自2017年以来,信宇人突破行业技术瓶颈并取得多项发明专利,历经数年的潜行打磨,成熟实现全工艺涂布方式,在近两年取得规模化量产和全面市场应用。
SDC涂布机不但自动化程度高,具有智能自学习能力,而且性能优良、功能性强。SDC涂布能满足满幅连续涂布、间隙涂布、条纹涂布、斑马涂布和田子涂布等全工艺涂布方式,成熟稳定,一致性高,广受电池企业认可与好评。
据悉,国内领先的多家头部锂电企业购置信宇人SDC涂布机,面对市场不断放大的3C和储能等行业市场,信宇人推出相应规格与标准的SDC涂布机,满足市场的广泛需求。目前,SDC涂布机已取得数十台批量供应,且有单批配套十余条生产线规模应用。
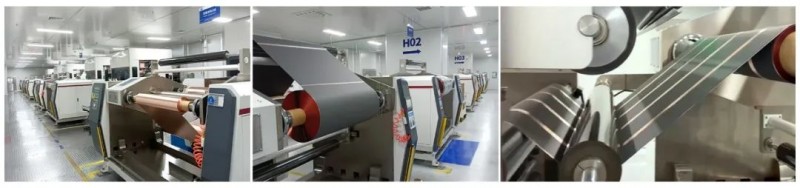
未来,随着SDC逐步市场化,更加趋向智能化、自动化、数字化、无人化,全力助力电池工厂走向工业4.0,推动实现更多更强的“熄灯工厂”、“零碳工厂”,紧迈“双碳”之步!