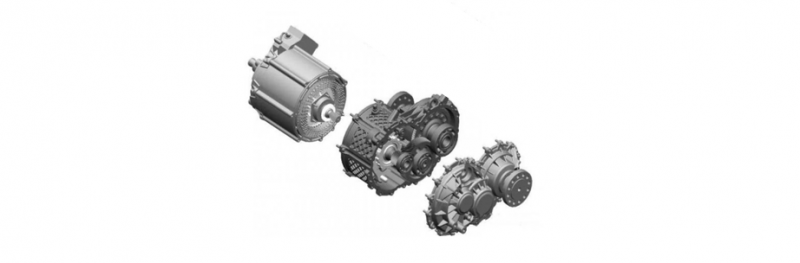
随着这些技术的不断成熟与应用,新能源汽车电驱动效率正逐步逼近理论上限,但是否已达“顶峰”仍是一个动态演进的过程,技术革新和材料科学的每次飞跃都有可能重新定义这个“顶”。因此,电驱动效率的探索之旅仍在继续,追求更高效率、更长续航、更优性能将是永恒的主题。本期笔者想跟大家聊聊电驱效率到顶了吗?以及各家产品的效率概况。
01.电驱的效率体系以及如何定义
电驱效率是指在理想情况下,电机输出的机械功率与输入的电功率之间的比率,电驱效率的衡量通常以百分比表示,比如90%的效率意味着有90%的电能被有效利用,剩余10%则转化为了损耗。新能源汽车电驱常说的最高效率,这个最高代表着什么有何意义?◎最高效率通常是指电驱在特定工作条件下转换电能为机械能的能力达到的最大百分比。
这意味着在该工作效率点,电机将输入的电能最大程度地转换为输出的机械转动能量,而损失在热量、振动等形式中的能量最小。这个效率值往往是在电动机和电控系统最优化配合、无额外负荷(除非载荷是测试的一部分)、理想温度和其他理想条件下测得的。最高效率代表了电驱系统可能达到的理论极限性能。
当然整体还需要遵循标准化的测试程序,因为要满足特定市场的法规要求,在测试电驱系统最高效率时,需要遵循相关标准的具体指导原则,如ISO标准或中国的GB标准以及其他行业认可的测试方法,以确保测试结果的可比性和可靠性。在评估电驱系统时,除了最高效率之外,平均效率、全工况效率以及在常用工况下的效率也非常重要,因为它们更能反映电驱系统在日常使用中的真实性能。
◎CLTC效率通常用来评估电动汽车电驱系统的整体能效,它是在模拟中国城市和公路实际驾驶条件下的效率,是基于CLTC工况循环测试得出的结果。这个效率值更接近于现实世界中电驱系统的表现,因为它考虑到了启动、停止、加速、减速等各种实际驾驶行为。与欧洲的NEDC(New European Driving Cycle)和全球统一的WLTP(Worldwide harmonized Light vehicles Test Procedure)测试循环有所不同。
CLTC效率评估电动汽车电驱系统的整体能效更能够反映电驱系统在复杂工况下的平均效率,包括电动机、逆变器、减速器以及其它相关组件在CLTC工况下的平均能量转换效率,因此对于评估电动汽车的能效和续航里程更有参考价值。从权威性和可信度的角度来看,CLTC效率和可靠性更好一点,更贴近实际驾驶条件。
最高效率虽然展示了电驱系统的潜力,但在实际应用中,车辆很少能在理想条件下持续运行,但是对于汽车制造商来说,最高效率也是评估电驱系统设计和技术创新的重要参数,特别是在研发阶段,它可以帮助工程师了解系统在极限条件下的性能边界。这两者结合来看,可以更全面的评估电驱系统的性能,最高效率反映得是技术潜力,而CLTC效率可反映出一定程度的实际应用效能。
02.各家电驱效率都达到了什么水平
电驱效率是整个电驱动系统的综合效率,包括电机、电控和减速器。电驱效率是系统中各部分效率的连乘积,反映了从电池到车轮整个能量转换过程的效率。这个因素很多,涉及到材料,工艺,结构各个方面。
汇川联合动力的第四代动力总成分为中功率版和高功率版,这两款第四代动力总成电驱系统,都是采用的高压系统,可支持最高工作电压到900V,支持升压充电Boost方案,最高效率超过95%,CLTC综合效率超过91%。
■控制器层面,汇川联合动力的第四代高压(800V)SiC单电机控制器开放度很高,支持各种模式的软件联合开发,最高效率≥99.6%。
■电机层面,汇川联合动力量产的纯电扁线电机主要是基于两个平台,OD180和OD210。这些电机CLTC综合效率都很高,其乘用车电机产品CLTC综合效率>97.2%。
◎联合电子的800V电桥配合先进调制算法和全局频率优化,最高效率可实现94.9%,CLTC综合效率可实现约91%。
■控制器层面,联电电子选择同800V技术更为适配的SiC芯片以大幅度提升效率,控制器单体最高效率达到99.5%。
■电机层面,联合电子是用的其特色的I-PIN绕组,其最高效率可达到97.5%,电机功率密度可达5.33kW/kg。
◎星驱科技的800V系列电驱产品,应用了模块化的结构设计理念,采用高效油冷技术、SiC控制器以及低摩擦轴承和脱开机构,系统效率92%。
■控制器层面,星驱科技的电机控制器产品,可适用于400V和800V电压平台,而且为了增加其产品的通用性,使用了一体化控制板,最高效率可达99.5%。
■电机层面,星驱科技的四款OD系列电机,同样适配于400V和800V电压系统,产品谱系功率范围涵盖80~450kW,其中最大的转速达到了24,000rpm,最大效率≥97.5%。
◎智新科技的iD3-200电驱动总成也是采用了平台化设计,提高了各模块通用性,其最高可拓展至10合1。最高效率达到了93.5%,CLTC综合效率超过89%,可以看出多合一对系统效率确实存在一定影响。
■控制器层面,智新科技具有多合一电路拓扑集成技术和高效的SiC功率模块驱动技术。
■电机层面,智新科技的电机绕组,采用无桥接、无环流绕组,并采取其他措施,如机械损耗抑制、磁钢损耗抑制和运行损耗抑制,通过各种手段尽可能降低损耗。目前已完成性能试验,峰值率达到98%。
◎广汽埃安的M25超级电驱通过电控算法效率提升、电机设计效率提升、轻负载传动系效率提升,达到了92.5%工况效率。
■控制器层面,M25超级电驱用的是900V高效碳化硅,采用铜排直连技术,低杂感高均流芯片布局来保证效率。
■电机层面,采用非晶合金材料,铁损系数远低于铁基硅钢等电工钢,降低电机50%铁芯损耗,让其电机工况效率提升至97.5%,电机最高效率达到98.5%。
03.是什么影响了电驱的效率
从上述各家产品可看出电驱效率受设计、材料、负载条件等影响,电控的效率与电力电子器件的选择、控制策略和散热设计有关,减速器的效率同样也受齿轮类型、齿轮材质、润滑情况和制造精度的影响。
◎采用SiC技术:SiC半导体器件,这种材料相比传统的Si基器件具有更低的开关损耗和导通损耗,能够支持更高的工作频率和电压等级,从而显著提高了逆变器和控制器的效率。SiC芯片能够承受更高电压,降低电力电子转换过程中的能量损失,这是达到高效率的关键之一。◎先进的调制算法:先进的调制算法,如空间矢量脉宽调制(SVPWM)或其他优化算法,这些算法能够更精细地控制电力电子变换器,减少开关损耗,进一步提高整体效率。
◎优化电机设计:采用永磁体分段设计,减少涡流路径,降低涡流损耗。提高铁磁材料的电阻率,比如加入硅,减少涡流损耗。设计低谐波的反电动势,减少磁滞损耗。优化绕组设计,优化气隙和磁路设计,减少磁饱和,提高磁通密度。
效率优先的逆变器及电机设计,配合先进调制算法和全局频率优化,加之电机和逆变器之间的紧密配合使二者能够在最佳工作点运行,这就是电驱产品效率的顶!