前言
伴随各类智能化技术应用成熟及其与制造业的快速融合,工业智能化进程正加速推进。在迈向智能制造热潮中,工厂底层生产设备的完整泛在联接性受到广泛关注。作为全球最大代工生产企业的富士康,在推进其成都工厂智能化建设的过程中,携手研华科技从底层数据采集与设备联网出发,一步一个脚印,最终实现总建筑面积171万平方米的超大厂区综合能源管控,为推进国内制造企业的智能化转型升级提供了借鉴。
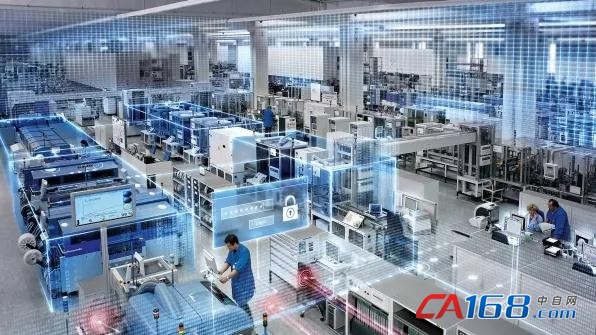
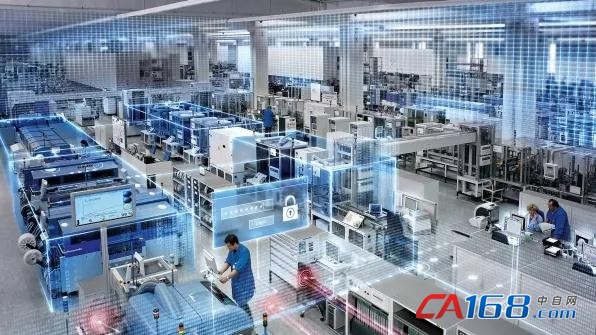
实现能源管控,数据采集先行
谈起富士康,大家头脑中的第一印象或许是其超大的工业园区和巨多的员工数量。以富士康成都工厂为例,这座位于中国西部地区的工厂是富士康在中国的第二大生产基地,拥有20万员工,占地2400亩,整个厂区由B、C、D三个生产区域组成了环形生产链条,共计30栋厂房。这种“巨无霸”的体量也导致了富士康在推进智能制造过程中,必须将节能减排和可持续发展列为重点发展策略。因为对于富士康而言,若能耗下降1%,带来的可能就是100%的利润回报。
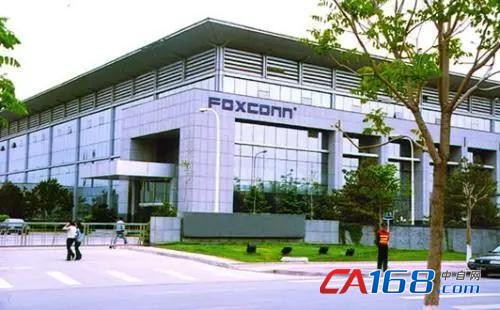
富士康工厂示意图
除成本效益外,随近年来人口红利的逐渐消失以及代工市场竞争的日益激烈,也使作为全球制造业“风向标”的富士康倍感压力,加速企业智能化和数字化的建设进程,率先以成都工厂开展环境友好、成本优化、节能增效和优化运营的能效管理工作。84栋厂房与建筑,25个能源站,17套中央空调系统、9套空压系统、17套变配电系统、3套氮气系统和2套锅炉蒸汽系统等共计2988个采集点设备状态亟待检测。然而在进行能源管控系统前期规划时,富士康却碰到了两大难点:
设备孤岛
工厂规模大、现场能耗设备众多。系统大部分各自为阵,没有实现数据的实时采集和互联互通。
数据繁多
信息化建牵一发而动全身,需通过平台化方式实现数据价值链传递,需端到端综合解决方案。
在富士康看来,工厂必须实现企业底层设备互联互通、能源数据自动化实时采集、能源使用监控管理以及能源信息精益分析,才能够通过数据分析发现能源异常,通过上层能源管理软件和底层自动化系统配合,真正堵住耗能漏洞。
携手研华,打通数据传输壁垒
富士康致力于实现世界级的智能化和可持续发展,因此需要一位优秀的合作伙伴携手前行,这也导致富士康花费了很长一段时间进行选型工作。在富士康看来,这位合作伙伴不仅要具备专业能源管理知识,拥有先进的产品技术,更重要的是还得具备深入车间系统的自动化经验。因为只有深谙车间生产工艺流程,才知道哪些数据需要采集、哪些工艺是耗能重点,才能为富士康提供“量身定制”的能源管理解决方案。
最终,富士康选择了研华科技作为综合能效管理合作伙伴。研华科技深耕智能工厂建设多年,拥有大量行业know-how,且对于用户的需求有着独到的理解,这也是促使富士康选择研华科技的首要原因;其次,研华科技不仅在全球范围内有着大量能源管理的成功实践,在底层数据采集和设备联网方面更是业内翘楚,可实现自底向上的全过程能源管控方案设计。最后,研华科技拥有奥宇节能这种优秀的方案实施方,具备成熟的项目方法论与丰富的经验和实践,能够保证项目按时圆满完成。
此外,研华科技与富士康在项目规划初期就构建了清晰的能源管理目标。经过双方反复分析后,富士康成都工厂综合能源管理体系架构以数据采集、数据传输、数据存储和应用层呈现,涵盖成都园区B区、C区、D区共25个能源站设备检测系统。
秉承最简化系统原则,研华科技通过边缘网关帮助富士康成都工厂底层打通各种协议互联,保持数据一致性向上传输。这就意味着富士康成都工厂能够采集车间产线、空压系统、制冷系统、水处理系统等包括来自第三方厂家的不同自动化系统里的信息和数据。从而帮助富士康成都工厂打通了横亘在各个系统之间的“数据孤岛”,让富士康成都工厂整个生产过程做到了可视化。
数据驱动,践行绿色智造
然而对于富士康而言,数据采集与设备联网只是基础,从数据中获取洞察并帮助企业提升运营效率才是目的。作为一家集能源管理与自动化为一身的供应商,研华不仅能提出端到端的体系架构,还能切实帮助富士康成都工厂在底层自动化层面实施改进措施。
如今,研华科技的综合能源管理系统能够帮助富士康成都工厂实时监控含能源站的1219块智能仪表、354套能量计/流量计和厂房145个流量计采集点,并对这些设备能源的消耗情况一览无余。除数据实时监控外,系统还能对能源消耗的历史数据进行周期性关联分析工作,确定到各个具体产线、设备,进一步辅助工厂编制能源计划,支持节能降耗方案或改善工艺的数据依据,最终实现工厂能源精细化管理。
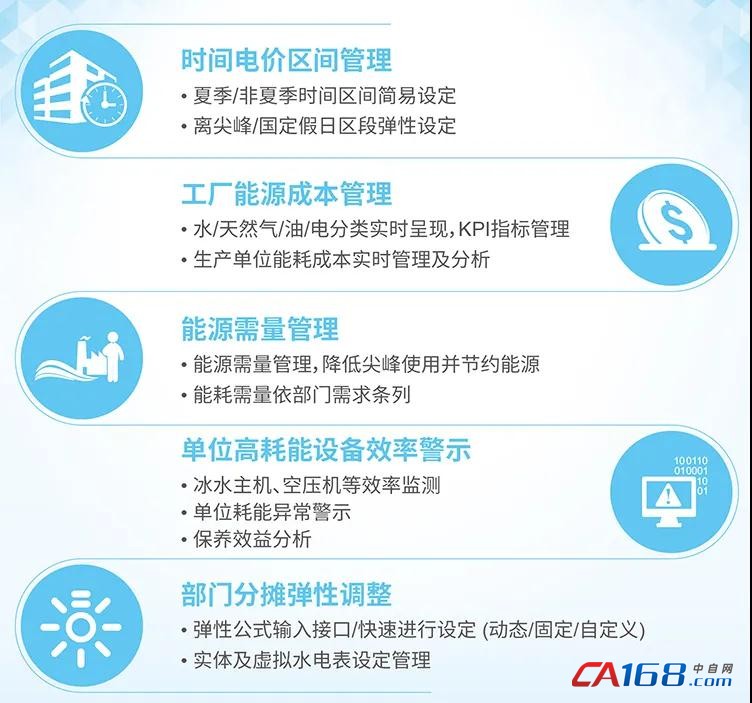
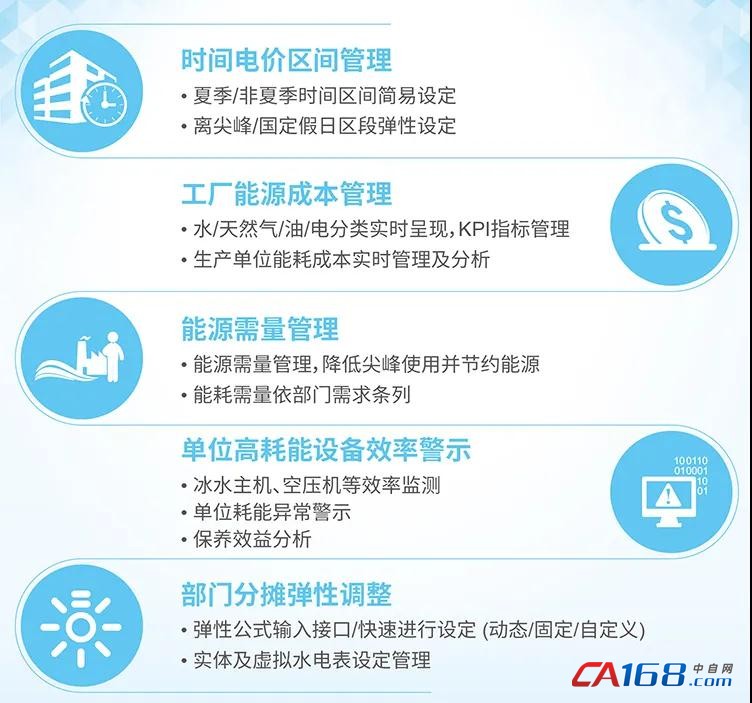
价值效益图
根据不同的季节和场景估算节能平均值,在实时综合能源管理系统后富士康成都工厂的总节能份额可达10-30%。过去生产基地能源站年耗电量约5亿千瓦时,现预计节电率将达到3%-5%,年节约电量约250万KWH,节约费用超过200万。值得一提的是,此次成都工厂、在动力联网监控、空调自控、水处理系统、锅炉自控等自动化领域的优化皆有涉及,真正意义上实现了综合能源管理系统的良好应用。
作为“十三五”规划收官之年,2020年初疫情给包括富士康在内的代工厂带来了不小的影响,主要体现在因疫情导致生产人员管理困难,以及消费市场对电子产品需求延迟。然而在富士康看来,以推进智能制造为主线,提高企业绿色化、智能化水平,提质增效的基调不会改变。未来,富士康也将继续携手研华科技,通过研华WISE-PaaS工业云平台进一步掌握实时生产状态、设备健康状况、产品和人员状况等,融入AI算法并据此进行生产排程、工艺优化、预测性设备维护和智能决策等,使各种各样的设备和产线变得更加智能,带来富士康成都工厂整体智能化水平的跃迁。